Compliance with the UN Global Compact
PEOPLE MAKE ALL THE DIFFERENCE
Nornickel received the international Randstad Award as the best employer in the metals and mining sector. The recognition came as a result of Nornickel's successful HR strategy.
Compliance with the UN Global Compact
Human rights
Human Rights Policy
UN Global Compact Principles
Principle 1: Businesses should support and respect the protection of internationally proclaimed human rights.
Principle 2: Businesses should make sure that they are not complicit in human rights abuses.
Respect for human rights is one of fundamental principles of Nornickel's operations. Being a socially responsible business, a major employer and a taxpayer operating in the territories with a mature legal culture, the Company promotes human rights. No operations are run in and nor raw materials procured from areas involved in military conflicts.
The Company complies with the applicable laws of the Russian Federation and other countries of its presence and respects both international standards for human rights protection and labour standards set out in the International Bill of Human Rights, the International Labour Organisation Declaration on Fundamental Principles and Rights at Work and the UN Guiding Principles on Business and Human Rights.
Nornickel takes steps to prevent and remedy any human rights violations, if any, across its assets and operations, including those engaged in exploration, production, concentration, refinement, output of end products, marketing and sales of non-ferrous and precious metals, as well as upon shut down of the Company’s mining operations, various production units and divisions across its locations. The Company expects its contractors to uphold human rights as well, which is formalised in a number of internal policies.
The protection of human rights is reflected in the Company's by-laws governing the HR, environmental, social and other matters.
The Company's President is responsible for ensuring that Nornickel respects human rights. The Company's employees are committed to respecting human rights and complying with the Russian and international laws and the Company's by-laws on human rights. The Company has a clear management structure alongside escalation and reporting lines to address human rights.
All of the Company’s new projects are screened for compliance with national and international legislation and, by extension, human rights laws. These checks span over ten of Nornickel’s functional divisions. The Company is mindful of human rights risks, so in addition to ensuring full compliance with the applicable requirements it also implements best practices: signs employment contracts and collective bargaining agreements, creates favourable work and rest conditions for its employees, including through carrying out new social infrastructure projects (housing, transport infrastructure, cultural and recreational facilities).
Information on alleged human rights violations is collected via Nornickel’s Corporate Trust Service, employee questionnaires, and sentiment surveys among local population. The Company guarantees confidentiality for whistle-blowers and respondents. Report statistics are reviewed by the Audit and Sustainable Development Committee of the Board of Directors on a quarterly basis.
In 2018, there were no incidents involving human rights violations. No disputes with the local population over land use were recorded. The Company does not plan any ramp-up in works related to acquiring land from the population and forced relocation.
Nornickel’s human rights PROTECTION PROCEDURES38
Interaction with indigenous northern minorities
103–2 103–3
Nornickel respects the rights, traditions, long-standing values and interests of indigenous northern minorities inhabiting the Company’s regions of operation. Nornickel's operations and companies located in traditional settlement areas of indigenous northern minorities include the Polar Transportation Branch, Norilskgazprom, Taimyrgaz and Norilsktransgaz. Nornickel’s key commitments to further strengthen and develop relations with indigenous northern minorities that benefit both parties are set out in the Indigenous Rights Policy,39 which is aligned with the Indigenous and Tribal Peoples Convention of the International Labour Organisation.
MM6
Representatives of the Group companies are members of indigenous northern minority commissions organised by local authorities.
Key areas of interaction with indigenous northern minorities
Nornickel’s key projects in the Arctic are focused on reducing air emissions, coastal cleanup and restoration of ecosystems, biodiversity preservation (including aquatic bioresources), development of transport infrastructure and Arctic shipping, ensuring transport accessibility of the Arctic, and implementing the Northern Supply Haul programme. Nornickel is active in promoting renewable energy sources in the Arctic, with the Taimyr HPP Cascade upgrade being one of the Company's major investment projects.
The Company has been supporting initiatives to improve living standards of the Taimyr Peninsula's indigenous people. The initiatives cover housing construction, maintenance and social projects in small and separated settlements on the Taimyr Peninsula, along with delivery of social aid for indigenous northern minorities and food for children of reindeer herders, and other projects.
To preserve national traditions and culture of indigenous northern minorities, the Company participates in staging the Big Agrish ethnic celebration, as well as annual professional festivals for tundra inhabitants on the occasion of Reindeer Herder's Day and Fisherman's Day.
Since 2017, Nornickel has been implementing the Comfortable Taimyr project as per its agreement with the Taymyrsky Dolgano-Nenetsky Municipal District authorities. Under the project, the Company is to fund the building of 2,500 sq m of housing in the Tukhard settlement, where housing stock disrepair was a serious issue. Pursuant to the agreement, Nornickel will build new and modern housing, as well as a utilities and social infrastructure with a school, kindergarten, hospital, boiler, power plant, and local treatment facilities. The location for the new housing was determined by a residents meeting based on their lifestyle.
In 2018, Nornickel and the Federal Agency for Ethnic Affairs (FAEA) signed an agreement on cooperation aimed at providing support to the indigenous peoples of the North who live in areas where the Company operates. Nornickel is supporting the Siberian Federal University’s work to revive the written language of the indigenous peoples of the North as part of the International Year of Indigenous Languages (2019).
In 2018, there was no record of the Company violating the rights of indigenous minorities. 411–1
Respect for human rights across Nornickel’s operations
Key human rights40 | Nornickel’s by-laws | Nornickel’s contribution | |||||||||||||
---|---|---|---|---|---|---|---|---|---|---|---|---|---|---|---|
Business Ethics Code |
Human Rights Policy |
Equal Opportunities Programme |
Working Conditions Policy 41 |
Occupational Health and Safety Policy |
Personal Data Policy |
Freedom of Association Policy |
Policy Regarding Support for Small and Medium Enterprises |
Local Community Relations Policy41 |
Environmental Policy |
Environmental Impact Assessment Policy |
Biodiversity Policy |
Renewable Energy Sources Policy |
Indigenous Rights Policy41 |
||
Right to life, freedom, and privacy, freedom from arbitrary arrest |
+
|
+
|
+
|
+
|
In 2018, the Company’s health and safety indicators were some of the best in the metals and mining industry, with LTIFR standing at 0.23 | ||||||||||
Right to health and medical assistance |
+
|
+
|
+
|
+
|
+
|
||||||||||
Right to protection from discrimination |
+
|
+
|
+
|
The Company does not tolerate discrimination on any grounds | |||||||||||
Right to freedom of association and collective bargaining |
+
|
+
|
+
|
+
|
The Company runs a social partnership framework, with collective agreements covering 80% of the workforce | ||||||||||
Right to work and to fair and adequate remuneration |
+
|
+
|
+
|
+
|
+
|
The average salary paid to Nornickel’s employees is well above Russia's average. The Company takes steps to secure jobs for vulnerable population groups and people with disabilities | |||||||||
Other labour rights (fair and favourable working conditions, social support, reasonable work schedule, ban on forced labour, regular paid vacations) |
+
|
+
|
+
|
+
|
The Company complies with the Russian Federation employment laws that are in line with the UN documents ratified by Russia. In 2018, Randstad Award recognised Nornickel as the most attractive employer in the Russian metals and mining industry. Forced labour is forbidden |
||||||||||
Right to education |
+
|
+
|
+
|
+
|
The Company runs a wide range of training courses for all of its personnel categories, providing career guidance and targeted support to educational institutions across its geographies | ||||||||||
Protection of family, maternity and childhood |
+
|
+
|
+
|
Child labour isforbidden. The Company respects and protects the rights of mothers and pregnant women. Its social programmes in the fields of housing, healthcare and culture aim to support and provide leisure opportunities for families |
|||||||||||
Freedom of movement |
+
|
+
|
+
|
+
|
The Company does not restrict the freedom of movement of its employees. It reimburses round trip travel expenses and baggage fees as part of the benefits package | ||||||||||
Right to shelter, right to own property |
+
|
+
|
+
|
+
|
The Company does not implement or plan to implement projects related to taking land from the population and forced relocation | ||||||||||
Right to a healthy environment |
+
|
+
|
+
|
+
|
+
|
+
|
The Company continuously works to reduce its environmental footprint and implements a comprehensive environmental policy | ||||||||
Rights of indigenous peoples |
+
|
+
|
+
|
The Company supports projects aimed at preserving the traditional lifestyle and culture of Taimyr’s indigenous peoples while fostering their economic and social development |
Labour relations
UN Global Compact Principles
Principle 3: Businesses should uphold the freedom of association and the effective recognition of the right to collective bargaining.
Principle 4: Businesses should uphold the elimination of all forms of forced and compulsory labour.
Principle 5: Businesses should uphold the effective abolition of child labour.
Principle 6: Businesses should uphold the elimination of discrimination in respect of employment and occupation.
Employees and social policy
103–2
Human capital is a key driving force behind the Company’s growth. In recognising this, the management of Norilsk Nickel Group seeks to create conditions that would boost employee performance and engagement, and exercises a comprehensive approach to HR management.
Respect for employees and their rights lies at the heart of the Group's business. The protection of human rights is guaranteed in a number of the Company's documents, including the Business Ethics Code, Personal Data Policy, Anti-Embezzlement Regulation and Human Rights Policy.
HR management assessment
103–3
To assess HR management and make efficient decisions, the Company continuously monitors HR metrics, analyses the structure of staff costs, labour productivity, and performance of social, adaptation and other programmes. The Company plans to introduce continuous monitoring of staff engagement and satisfaction.
Staff composition
Nornickel received the international Randstad Award as the best employer in the metals and mining sector. The recognition came as a result of Nornickel's successful HR strategy.
This was not the first time that Nornickel won this prestigious award. In 2016, the Company received Randstad's Grand Prix as the Best Employer in the Russian metals and mining industry.
HR management
Guided by the provisions of international declarations and conventions, the Constitution and the Labour Code of the Russian Federation, the Company absolutely excludes employment of children, and employment of minors in harmful and/or dangerous working conditions. The Company strictly complies with the rules prohibiting employment of women in harsh and dangerous working conditions in the mining industry. The Company respects and protects the rights of working mothers.
The Company provides its employees with equal opportunities to exercise their labour rights regardless of their gender, age, race, nationality, origin, property, social and official status, place of residence, religious beliefs and political views, as well as other circumstances unrelated to their professional skills. All employees have equal opportunities to unlock their professional potential; their performance evaluation is impartial and fair. Employees are selected and promoted solely on the basis of their professional abilities, knowledge, and skills.
The Company creates programmes for the development and social support of its staff and pursues the social and economic rights of its employees, including the right for social support, education, family welfare, shelter, freedom of creativity, and participation in cultural life. The Company respects its employees’ trade union rights, which form an integral element of the right to association and the right to negotiation.
The Company employees’ working hours (weekly hours of work, daily (shift) hours of work, work start and end time, break start and end time, shifts per day, working/non-working day alternation, specialised working time patterns for certain categories of employees, including night and overtime work) are established by internal labour regulations approved by the Company with due regard to the opinion of the trade union. The Company has a standard working week of 40 hours as determined by the applicable Russian laws and regulations. Employees involved in harsh, hazardous and/or dangerous work enjoy a reduced working week of not more than 36 hours. Women employed in the Far North and equivalent areas are accorded 36 hours of work per week unless reduced by Russian laws and regulations. The Company arranges for accurate time and attendance control for each employee.
The Group's average headcount in 2018 was 74,926 employees in Russian companies, and 975 employees in foreign subsidiaries.
The headcount decrease across the Russian operations by 3.9% y-o-y was due to the programme to improve labour productivity and reduce costs.
102–8
The headcount41 of the Group’s Russian companies as at the year-end stood at 74,960. Most of employees work full time (>99%) and on the basis of unlimited employment contracts (>96%). As at the end of 2018, there were 541 employees working under civil contracts.
Group personnel structure by territory, %
66.9 |
Norilsk Industrial District (NID) |
16.6 |
Kola Peninsula Industrial District (Murmansk Region) |
4.647 |
Krasnoyarsk Territory (excluding NID) |
4.456 |
Trans-Baikal Territory |
6.164 |
Moscow and other regions of Russia |
1.284 |
Outside Russia |
Headcount of the Group's foreign operations, employees
Europe |
330 |
Asia |
13 |
North America |
10 |
Australia |
5 |
Africa (South Africa) |
605 |
Africa (Botswana) |
12 |
Personnel structure by category, %
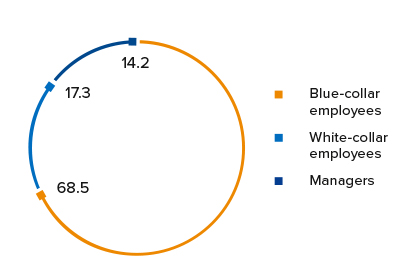
Personnel structure by gender,42 %
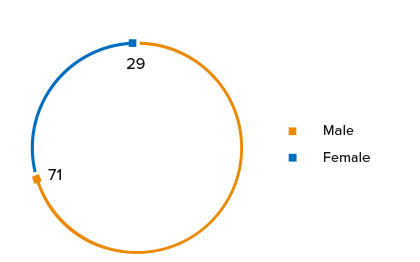
Personnel structure by education, %
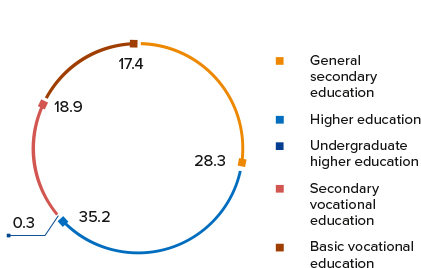
Key personnel turnover indicators43 401–1
Indicator |
2013 |
2014 |
2015 |
2016 |
2017 |
2018 |
---|---|---|---|---|---|---|
Employments |
10,103 |
13,220 |
15,607 |
15,166 |
11,262 |
14,901 |
Employee inflow ratio,44 % |
12.2 |
16.5 |
19.1 |
18.8 |
14.6 |
19.9 |
Separations |
13,738 |
12,812 |
14,277 |
15,413 |
15,232 |
16,918 |
Employee turnover,45 % |
12.1 |
11.3 |
10.7 |
10.5 |
10.3 |
10.2 |
Employee outflow ratio,46 % |
16.7 |
15.6 |
17.1 |
19.2 |
20.0 |
22.6 |
103–2
The Company is a major employer in the Norilsk Industrial District and the Kola Peninsula and as such has a significant impact on these regions’ labour markets. The Company has no policies in place providing for the preferential hiring of locals; staff selection takes into account candidates’ skills, qualifications, and education.
In 2018, the Company employed 509 new permanent staff members from other regions of Russia.
202–2
The share of top executives representing local communities stood at 98.0%. Russian citizens accounted for 99.6% of the Russian operations' total headcount.
Headcount by employment, gender and region, employees
102–8
Indicator |
2018 |
||
---|---|---|---|
Total |
Male |
Female |
|
Total headcount in Russia as at the latest reporting date |
75,501 |
53,355 |
22,146 |
Contractors working under civil contracts as at the latest reporting date |
541 |
239 |
302 |
Employees as at the latest reporting date |
74,960 |
53,116 |
21,844 |
Employees working under fixed-term contracts (temporary and seasonal jobs) as at the latest reporting date |
2,966 |
1,599 |
1,367 |
in the Norilsk Industrial District |
1,647 |
ХХХ |
ХХХ |
in the Krasnoyarsk Territory (except for NID) |
46 |
ХХХ |
ХХХ |
in the Kola Peninsula Industrial District (Murmansk Region) |
155 |
ХХХ |
ХХХ |
in Moscow and other regions of Russia |
620 |
ХХХ |
ХХХ |
in the Trans-Baikal Territory |
498 |
ХХХ |
ХХХ |
Employee working under unlimited contracts (permanent jobs) as at the latest reporting date |
71,994 |
51,517 |
20,477 |
in the Norilsk Industrial District |
48,932 |
ХХХ |
ХХХ |
in the Krasnoyarsk Territory (except for NID) |
3,295 |
ХХХ |
ХХХ |
in the Kola Peninsula Industrial District (Murmansk Region) |
12,502 |
ХХХ |
ХХХ |
in Moscow and other regions of Russia |
4,495 |
ХХХ |
ХХХ |
in the Trans-Baikal Territory |
2,770 |
ХХХ |
ХХХ |
Full-time employees as at the latest reporting date |
74,118 |
52,563 |
21,555 |
Part-time employees as at the latest reporting date |
99 |
31 |
68 |
Number of employees who joined and left the Company by gender, age, and region of operation in 2018, employees
401–1 401–3
Indicator |
2018 |
---|---|
Employments |
14,901 |
male |
11,198 |
female |
3,703 |
29 y. o. and below |
4,897 |
30 to 44 y. o. |
6,248 |
45 y. o. and above |
3,756 |
in the Norilsk Industrial District |
8,535 |
in the Kola Peninsula Industrial District (Murmansk Region) |
2,619 |
in the Krasnoyarsk Territory (except for NID) |
694 |
in Moscow and other regions of Russia |
1,456 |
in the Trans-Baikal Territory |
1,597 |
Separations |
16,918 |
male |
12,672 |
female |
4,246 |
29 y. o. and below |
4,212 |
30 to 44 y. o. |
6,764 |
45 y. o. and above |
5,940 |
in the Norilsk Industrial District |
10,434 |
in the Kola Peninsula Industrial District (Murmansk Region) |
2,907 |
in the Krasnoyarsk Territory (except for NID) |
917 |
in Moscow and other regions of Russia |
1,074 |
in the Trans-Baikal Territory |
1,586 |
Employee outflow ratio by region in 2018, %
Indicator |
2018 |
---|---|
Kola Peninsula Industrial District (Murmansk Region) |
23.0 |
Krasnoyarsk Territory (excluding NID) |
27.4 |
Moscow and other regions of Russia |
21.0 |
Norilsk Industrial District (NID) |
20.6 |
Trans-Baikal Territory |
48.547 |
Employee inflow ratio by region in 2018, %
Indicator |
2018 |
---|---|
Kola Peninsula Industrial District (Murmansk Region) |
20.7 |
Krasnoyarsk Territory (excluding NID) |
20.8 |
Moscow and other regions of Russia |
28.5 |
Norilsk Industrial District (NID) |
16.9 |
Trans-Baikal Territory |
48.9 |
Employee outflow ratio by gender and age in 2018, %
Indicator |
2018 |
---|---|
Employee outflow, total |
22.6 |
Employee outflow, male |
23.9 |
Employee outflow, female |
19.4 |
Employee outflow, 29 y. o. and below |
29.0 |
Employee outflow, 30 to 44 y. o. |
18.2 |
Employee outflow, 45 y. o. and above |
23.5 |
Employee inflow ratio by gender and age in 2018, %
Indicator |
2018 |
---|---|
Employee inflow, total |
19.9 |
Employee inflow, male |
21.1 |
Employee inflow, female |
17.0 |
Employee inflow, 29 y. o. and below |
33.7 |
Employee inflow, 30 to 44 y. o. |
16.8 |
Employee inflow, 45 y. o. and above |
14.8 |
Employees on maternity and/or childcare leave in 2018 401–3
Indicator |
2018 |
---|---|
Employees on maternity and/or childcare leave as at the year-end |
1,781 |
male |
38 |
female |
1,743 |
Employees back from maternity and/or child care leave over the year |
878 |
male |
42 |
female |
83 |
Personnel development
The Company views its people as its key asset and keeps investing in their professional and personal development. Our personnel development policy focuses on creating an environment that helps fully unlock the professional and creative potential of each employee while also fostering team spirit and commitment to the Company’s goals. With this in mind, the Company plans the professional and career growth of its people, builds a talent pool for managerial positions, trains and promotes pool members.
Training
103–2 404–2
With our reconfigured production cycle, modernised operations, new technologies and approaches, we need to make sure our employees meet the new expertise, skill and competency requirements. This is why training plays an important role in Nornickel's personnel development.
The Company introduced staff training programmes across all functional areas and staff categories — from top managers to workers. Training is an ongoing process that takes place throughout an employee's career.
MMC Norilsk Nickel has the Model Regulation on Professional Training in place, which the Group companies use a basis to develop their internal training regulations.
Nornickel launched the IamHR development programme for HR professionals. The programme seeks to improve their professional skills, strengthen interactions between business and HR, and educate the staff about state-of-the-art solutions and available practices in HR management.
The Group's employees can benefit from free staff training, retraining, skills improvement, and internship programmes funded by the Group companies. The Company engages external education providers (universities, professional development institutions, research institutes, training centres, and consultants), and trains employees at its own corporate training centres. The Group’s key training hubs are the Norilsk Nickel Corporate University (Norilsk) and the Kola Staff Development Centre (Monchegorsk), which provide training to more than 52,000 employees a year.
In 2018, 54 key employees, heads of production units and the Head Office of Nornickel completed an innovative operating efficiency training programme organised jointly with Moscow's Skolkovo School of Management. The programme aims to make production management more efficient, among other things, by developing key managerial competencies, looking into the latest technologies, approaches and best practices in the area, and identifying ways to apply them.
Key personnel training indicators 404–1
Indicator |
2014 |
2015 |
2016 |
2017 |
2018 |
---|---|---|---|---|---|
Employees covered by professional training, retraining and skill improvement, thousand |
54.1 |
63.1 |
70.0 |
95.0 |
87.549 |
|
31.5 13.8 8.8 |
35.3 18.2 9.5 |
37 22 11 |
54 26 15 |
43.3 27.4 16.8 |
Total training man-hours, thousand |
5,079.2 |
5,824.1 |
5,666 |
6,630 |
4,508.7 |
Average annual hours per employee trained |
93.8 |
92.2 |
80.8 |
70 |
51.6 |
Average annual training hours per employee (based on average headcount) |
63.5 |
71.2 |
69.8 |
85 |
60.2 |
|
- - - |
- - - |
77.9 72.4 31.9 |
95 83 44 |
62.2 76.7 38.7 |
Professional training costs, RUB mln |
661.5 |
669.1 |
760 |
896 |
1,022.2 |
Costs per employee trained, RUB |
12,220 |
10,589 |
10,841 |
9,459 |
11,687 |
Talent pool
The reporting year saw the Company continue to roll out the talent pool management programme at its Norilsk site. We launched a training and development programme for talent pool members and their mentors based on cutting-edge education technologies and a combination of classroom and online sessions.
On top of that, we provided the pool members with a roadmap of development activities and recommendations on how to strengthen competencies covered by the corporate model.
Over the year, Polar Division and the Kola Peninsula facilities introduced an SAP HCM-powered system to automate and boost the efficiency of talent pool management, among other things, through the consolidation of relevant data into a shared database.
Development projects for target personnel categories
Target category |
Project |
Priorities |
Coverage in 2018, thousand employees |
---|---|---|---|
Highly qualified workers |
Mentor Academy |
|
7.6 |
Line managers (foremen) |
Foreman University |
|
4 |
Young employees aged 18 to 35 |
Leader, movement of young professionals |
|
18 |
Career guidance, cooperation with educational institutions
The Company runs an array of programmes to attract and train staff. The major ones are the Career Start-Up internship programme, Conquerors of the North internal case competition, and the First Arctic leadership programme. The Company’s career guidance initiatives are integrated into the relevant regional programmes and target children and youths aged below 35.
The Company prioritises the following training areas:
- underground (subsurface) ore mining;
- mine surveying;
- mineral processing;
- mining electrification and automation;
- mine and underground construction;
- industrial and civil construction;
- ground vehicles, hoisting/conveying and road machinery;
- mining machinery and equipment;
- power and electrical engineering;
- operation of transportation vehicles and systems.
The Company has established close cooperation with educational institutions. Its facilities invite students to take part in the Career Start-Up programme of pre-graduation internships and work placements. The programme cooperates with 25 Russian universities. In 2018, 311 students joined the programme, with 118 top-performing ones awarded Nornickel’s corporate scholarship and 88 hired by the Company after graduation. In 2019, the Company’s facilities will offer internships to 312 students.
In summer 2018, more than 200 students took part in the Conquerors of the North team business game to try and tackle some of the Company’s real tasks. Nornickel was the first metals and mining company in Russia to use this methodology with students.
The Company places a strong emphasis on engineering education in Russia, contributing to the promotion of relevant professions. In 2018, we supported Cup Technical and Metal Cup Championship 2018, case-solving championships among students of Russian technical universities. During the contest, students dealt with cases related to Nornickel’s operations, gaining insight into the Company’s business processes.
Also, we run a number of career guidance events for schools, such as the Arctic.PRO R&D marathon, ARCTIC WAVE festival of R&D discoveries, I Make competition for young inventors, and the School of Urban Competencies, attended by over 4,000 school children annually.
Incentives and rewards
Remuneration policy goals |
Remuneration policy principles |
---|---|
|
|
In 2018, the Company implemented the job grading framework linking each job and related remuneration to its significance for business processes. This is a key tool that should help the Company to secure maximum return on investment in human capital, engage and retain the best talent. Grading relies on the points factor method of job evaluation that takes into account knowledge and skills, the complexity of tasks, and the level of responsibility.
Remuneration package across the Group's Russian operations in 2018, %
Key compensation indicators 202–1
Region |
Remuneration package, RUB thousand |
Average monthly salary, RUB thousand |
Regional payroll percentage of the aggregate payroll, % |
Minimum monthly compensation to statutory minimum monthly wage,50 % |
Statutory minimum wage |
---|---|---|---|---|---|
Group average |
- |
111.6 |
- |
- |
- |
Kola Peninsula Industrial District (Murmansk Region) |
89.1 |
82.4 |
12.3 |
1.00 |
25,675 |
Krasnoyarsk Territory (excluding NID) |
56.2 |
54.1 |
2.3 |
1.0 |
10,592 |
Moscow and other regions of Russia |
316.3 |
293.5 |
16.6 |
1.82 |
18,781 |
Norilsk Industrial District (NID) |
118.0 |
107.7 |
65.2 |
1.02 |
29,024 |
Trans-Baikal Territory |
90.2 |
86.9 |
3.5 |
1.02 |
16,745 |
Average monthly salary in Nornickel Group, RUB THOUSAND
Year |
RUB |
---|---|
2014 |
75.4 |
2015 |
84.9 |
2016 |
94.2 |
2017 |
104.1 |
2018 |
111.6 |
Employee awards
To motivate and financially incentivise its employees to work efficiently and productively, and deliver the highest operational results, the Company has put in place a structured system of incentives and rewards of various categories and levels: government awards, ministry and agency awards, regional and municipal awards, corporate Nornickel awards, and internal awards granted by Norilsk Nickel Group
companies.
In 2018, MMC Norilsk Nickel approved its Award Policy, which sets out the goals, principles, rules, requirements and limitations of the Company's awarding activities.
Underlying principles of the Award Policy:
- Fair and transparent procedure for nominating and rewarding employees. The Company uses fair, relevant and transparent criteria to ensure that the awarded employee and their colleagues clearly understand which achievements are recognised, and create a perception that the award is fair and well deserved.
- Award relevance, attainability and importance. The Company maintains a balance between employees' aspirations to be rewarded and attainability of the awards through an objective distribution of award quotas, transparent and fair procedures, significant material and non-material incentives, and award events.
- Communication and awareness. The Company makes available the documents governing the Award Policy and the list of award categories and awards while also providing for visible and clear nomination and awarding conditions, criteria and procedures.
- Maximum awareness of all employees about award winners. The award process is open and enjoys various types of information support. Information on the awardees is communicated to employees via all internal communication channels.
- Frequency. Award campaigns and events are evenly distributed throughout the calendar year.
- Equal opportunities for employees working at different locations and positions to be nominated and awarded. The Company ensures there is no gender, ethnic, or religious discrimination in the nomination and awarding of employees.
- Development of employees in line with strategic priorities and corporate values through better use of their potential and motivation to improve their professional skills.
The Company recognises employees for their outstanding professional achievements and contribution, innovations that drive growth, add economic value or boost the operating efficiency of a specific facility or the Group in general, efforts going beyond formal agreements with the Company, and business improvement initiatives. The Company praises and distinguishes employees showing exceptional production, engineering and managerial competencies by awarding those who delivered remarkable operational or management performance and contributed a lot to advancing production.
To recognise employee achievements, the Company has a range of corporate awards, including:
- MMC Norilsk Nickel badge of honour;
- MMC Norilsk Nickel titles of honour: Best Executive, Best Specialist, Best Worker;
- MMC Norilsk Nickel certificate of honour;
- MMC Norilsk Nickel certificate of commendation.
In 2019, according to the Award Policy a number of special titles of honour were introduced:
- Best Young Talent;
- Best Start of the Year;
- Change Leader;
- Best Health and Safety Head;
- Best Health and Safety Line Manager;
- Best Health and Safety Specialist;
- Best Health and Safety Compliant Worker;
- Best Inventor;
- Corporate Life Leader.
In addition to a corporate award, the employee receives a one-off bonus. MMC Norilsk Nickel badge of honour, the highest corporate award, entitles its owner to a one-off payment, as well as a lifetime corporate pension.
The best employees may be nominated for agency (industry) and government awards. The Company welcomes the recognition of its employees’ accomplishments by the government and its agencies, while also distributing its own accolades for prodigious operational and management achievements, and significant contribution to production growth.
In 2018, 4,304 Company’s employees were awarded for outstanding production results and many years of diligent service, including 83 and 286 honoured with government and ministry/ agency awards, respectively, 1,664 who received awards from regional and municipal authorities, 275 and 1,996 who were granted corporate and local awards of the Group companies.
Social policy
The social policy of Norilsk Nickel Group is implemented in a consistent manner based on the feedback principle. To make changes to the existing programmes, develop new ones and close those that have achieved their goals and objectives, the Company conducts an in-depth comprehensive review and selects the best solutions in terms of social interests, economics of the Company, and the interests of its employees. We are constantly monitoring the performance of our programmes to ensure timely identification of possible weaknesses.
The social package includes the following benefits and compensations:
- health resort treatment and vacation to employees and their families at subsidised prices;
- payment of return travel and baggage costs to a place of vacation to employees in the Far North and equivalent areas, and their families;
- one-off financial aid in the face of certain life events, or hardships;
- additional employee pensions and other types of social guarantees under the existing collective bargaining agreements and local regulations.
Social expenses, RUB mln
Indicator |
2018 |
2019 |
|
---|---|---|---|
Plan |
Actual |
Plan |
|
Health resort treatment and vacations of employees and their families |
2,040 |
1,947 |
1,818 |
Reimbursement of round trip travel expenses and baggage fees to employees and their families |
3,186 |
3,355 |
3,269 |
Pension plans |
1,186 |
961 |
1,220 |
Housing programmes |
6,760 |
6,252 |
3,113 |
Relocation assistance to new employees |
345 |
209 |
322 |
Social projects for employees (development of target categories, sporting events and holiday celebrations) |
600 |
630 |
657 |
Voluntary health insurance |
238 |
347 |
826 |
Financial aid and additional benefits to retired and former employees and their families |
255 |
201 |
260 |
Other payments and social expenses (healthcare services, severance pay, etc.). Social payments (excluding travel expenses) |
1,476 |
1,791 |
1,371 |
Expenses related to social programmes and benefits for employees |
16,086 |
15,693 |
12,855 |
Health improvement programmes
For many years, Norilsk Nickel Group has been running a programme of rehabilitation and health resort treatment for its employees and their families. The harsh climate of the Far North and the nature of the Group's operations require special care of the employee health, which makes health improvement and wellness a priority of the corporate social policy.
Key health improvement programmes |
Participants |
---|---|
Zapolyarye Health Resort (Sochi) |
11,026 |
Kolsky Health and Spa Centre (Monchegorsk) |
1,693 |
Non-corporate health resorts, including: |
4,341 |
Rossiya and Belokurikha health resorts (Altai Territory) |
582 |
Rosa Springs Health Resort (Sochi) |
3,450 |
other non-corporate health resorts |
309 |
Vacation for children (including Anapa and Bulgaria) |
1,391 |
International vacation programme (Bulgaria, Greece) |
6,180 |
Total participants |
24,631 |
Co-Funded Pension Plan programme
201–3
Co-Funded Pension Plan, a corporate private pension programme, has been running since 2007. As at the end of 2018, it saw 13,900 participants from among employees of 22 companies, with over 6,000 receiving pensions.
The programme provides for two pension plans: Parity and Corporate. Under the Parity Plan, pension savings are co-funded by the employee and the Company on a par (equal) basis. The Corporate Plan is designed for highly skilled employees and/or employees with highly sought-after occupations; within this plan, the Company finances private pension plans for such employees. In 2018, an average participant contribution amounted to 2.9% of the employee’s salary or the Group’s monthly average of RUB 3,000.
Participants of the Co-Funded Pension Plan in 2018
Indicator |
2018 |
2019 (plan) |
---|---|---|
Total participants |
13,916 |
15,473 |
Kola Peninsula Industrial District (Murmansk Region) |
2,351 |
2,760 |
Krasnoyarsk Territory (excluding NID) |
0 |
0 |
Moscow and other regions of Russia |
20 |
25 |
Norilsk Industrial District (NID) |
11,545 |
12,688 |
Trans-Baikal Territory |
0 |
0 |
Co-Funded Pension Plan highlights
Indicator |
2018 |
---|---|
Total Company costs, RUB thousand |
483,628.9 |
Participant’s contribution |
|
Average contribution per participant, % of wages |
2,89 |
Average monthly contribution per participant, RUB |
2,999 |
Company’s contribution under the Parity Plan |
|
Average contribution per participant, % of wages |
2,88 |
Average monthly contribution per participant, RUB |
2,976 |
Housing programmes
In the reporting period, the Company continued with its Our Home and My Home corporate social programmes launched back in 2010 and 2011, respectively.
The programmes now run as a single Our Home/My Home programme covering the employees of Polar Division, Polar and Murmansk Transport Divisions, Kola MMC and 18 more Group companies operating in Norilsk, the Taimyrsky Dolgano-Nenetsky Municipal District and the Murmansk Region. Since the start of the programme, 3,804 apartments have been granted to the Company’s employees. In total, the Company has purchased 4,348 ready-for-living apartments, including 522 in 2018. As part of the programmes, the Company purchases ready-for-living apartments in various Russian regions at its own expense and provides them to eligible employees under co-financing agreements. The Company pays up to a half of the apartment cost (but in any case no more than USD 54,000), with the rest paid by the employee within a certain period of employment with Nornickel Group (from five to ten years). The cost of housing remains unchanged for the entire period of the employee’s participation in the programmes. Ownership rights are registered at the end of the programmes, but the employee may move in immediately after receiving the apartment.
In 2014–2018, the apartments were purchased in Moscow and Tver regions, as well as in the Krasnodar Territory, with the Company seeking to buy properties located in close proximity to enhance the employees' living standards by developing additional infrastructure and optimising the scope of maintenance tasks assigned to the property management company.
Assistance to employees in acquiring housing
The Company also runs the Corporate Social Subsidised Loan Programme for Employees of Nornickel that was phased from a pilot to an ongoing project. This programme was developed primarily as a tool to retain highly qualified staff, with employees at Polar Division and Kola MMC entitled to an interest-free loan to make a down payment and to reimbursement of a certain share of interest on their mortgage loan. Overall, more than 200 employees took part in the programme.
Support to new employees
Nornickel provides financial support to newly employed staff relocating to Norilsk and the Taimyrsky Dolgano-Nenetsky Municipal District, including young specialists, workers, engineering staff and managers.
The Company reimburses the following expenses of newly employed staff:
- travel expenses;
- baggage transportation;
- living costs for the first three years.
On top of that, the Company also pays a one-time relocation allowance to support the employee at the new place of work.
With 379 employees joining the relocation support programme in 2018, it now boasts 1,520 participants.
Sporting and mass public events programme
The Company promotes sports and healthy lifestyle to solidify the corporate team spirit and maintain a positive work environment. It organises sporting events and competitions attended by its employees, their families, and the local community.
The events include the annual Polar Division Olympics, Kola MMC Olympics in 16 sports, Norilsk Nickel Ski Track health marathon, “Dad, Mum and I — a Sporty Family” corporate competition, swimming, ice hockey, futsal, volleyball, basketball, alpine skiing, snowboarding competitions, and sport events dedicated to the Metallurgist Day and other high days and holidays.
To promote amateur hockey, Norilsk hosted the Night Hockey League (Northern Conference) in 2018, with 11 teams comprising Nornickel employees among the participants.
The reporting year saw some 27,000 people take part in Nornickel's sports events. Also, the Company's facilities in Norilsk feature gyms.
Programmes supporting former employees and their families
The ongoing support of its former employees is part of the Company’s corporate social policy.
The Company's Veterans programme has been designed to support unemployed pensioners who permanently reside in Norilsk. The terms of participation depend on the employee’s length of service or permanent disability status. Financial aid is paid from the charitable contributions made by the Company.
Under the programme of financial aid to retiring employees, benefits are provided to employees at the time of retirement, with the amount linked to their employment period.
The Pensioner Financial Aid Fund extends financial aid to former employees who retired prior to 10 July 2001 provided they had been employed at the Company’s divisions for more than 25 years and permanently reside outside of the Norilsk Industrial District. The Fund relies on voluntary monthly contributions from employee salaries and equal charitable contributions from the Company's budget.
The Company also provides targeted assistance to its former employees and their families to pay for health improvement and medications, funeral services, and helping in financial distress.
Support of employees with disabilities
The Company fully complies with the legislation regarding employment of people with disabilities. As per the employment quotas that vary depending on the region and company size, the share of such employees may come up to 2% of the average headcount.
The Company takes steps to secure jobs for people with disabilities and ensure necessary working conditions, including work and rest schedule, annual and additional paid leaves, and specialised workspace equipment.
Occupational health and safety
103–2
Occupational health and safety is one of Nornickel’s strategic priorities. The Company is aware of its responsibility for ensuring health and safety of all employees engaged in its operations, both its own and third party.
Nornickel’s Occupational Health and Safety Policy gives precedence to the life and health of employees over operational performance while also demonstrating the Company’s commitment to creating a safe and healthy environment and fostering sustainable employee motivation for safe workplace behaviour.
Zero work-related fatalities and an ongoing reduction in overall workplace injuries are the Company's key strategic priorities in OHS.
Health and safety management
Nornickel put in place 15 corporate occupational health and safety (OHS) standards:
- Prevention and Control Activities with regard to Health and Safety Processes;
- Safety Behaviour Audit;
- Power Source Insulation;
- High Altitude Operations;
- Provision of Personal Protective Equipment;
- Safety Requirements for Boarding and Alighting Company’s Motor Vehicles during Inter-Facility Transportation;
- OHS Communication, Accounting and Reporting Procedures;
- Accident Investigation;
- Procedure for Organising and Conducting High-Hazard Operations;
- Safety Requirements for Interaction of Vehicles and Pedestrians at Production Sites and Facilities;
- Hazard Identification, Assessment and Management of Occupational Health and Safety Risks;
- Management of Technical, Technological, Organisational and HR Changes;
- Requirements for Demarcation of Hazardous Areas and Visualisation of the Working Space;
- Contractor OHS Management;
- OHS Contest Arrangements.
103–2
The Company continues to improve OHS management processes, among other things, by drafting and implementing corporate standards. In 2018, the Company proceeded with the projects to control risks and implement the framework to manage technological and organisational changes. The projects seek to build an effective system to continuously identify and control significant OHS risks and changes within the Group.
The reporting year saw the Company start implementing an automated system for OHS management monitoring, with its first stage put on stream at Kola MMC, Pechengastroy, and the Head Office.
Nornickel regularly takes preventive and control measures, including:
- second-party OHS management audits (cross-company audits of the Group companies involving the OHS heads and experts from other Group companies). There were 45 audits in 2018;
- internal OHS management audits;
- activities as part of the OHS monitoring system at each facility, including:
- multi-stage control;
- ad hoc, targeted and comprehensive OHS inspections;
- safety behaviour audits;
- compliance and certification audits as part of the OHSAS management system;
- independent external audits of the corporate OHS management system and occupational safety culture.
Prevention of occupational diseases
The Company implements measures to prevent occupational diseases. Employees undergo compulsory pre-employment, regular and ad hoc medical examinations and check-ups organised at the Company's expense. Those that have contact with hazardous materials are subject to additional examinations held at least once in five years by occupational pathology centres or other organisations authorised to conduct pre-employment and regular check-ups. These serve to assess occupational health fitness and determine if the disease is job-related. In 2018, the Group's costs related to medical examinations and maintenance of medical aid posts amounted to RUB 437.1 mln and RUB 221.5 mln, respectively.
The Company’s facilities have their own medical aid posts to perform pre-shift and pre-trip checks and provide medical assistance to employees.
To automate the process, the Company started introducing an electronic health check-up system n 2018, piloted at Kola MMC and GRK Bystrinskoe.
The Company provides employees working in harmful and hazardous conditions with free foods, milk, and other equivalent food products for therapeutic purposes in compliance with the applicable Russian legislation and corporate policies. In 2018, foods and milk costs across the Group amounted to RUB 1,247.9 mln.
In case of hazardous production factors identified by the special assessment of working conditions, the Company provides employees with personal protective equipment (PPE).
In 2018, the Company put in place Alcoframes, contactless breath alcohol screening devices, to prevent intoxicated employees from accessing production facilities. The devices are running at Polar Division (Copper Plant), Medvezhy Ruchey, GRK Bystrinskoe and Norilsk Support Complex. The Company continues to work in this area.
Contractor safety management
Contractor operations (repair, construction and installation works at the existing facilities) are classified as high-hazard and governed by the respective corporate standard. Work permits, operations certificates and work execution plans (process sheets, guidelines, etc.) must contain safety requirements to be met when organising and performing work. The Company checks compliance with these requirements during each shift. Prior to commencement of work, contractors’ staff receive pre-job and ad hoc health and safety briefing, including security measures set forth in work execution plans.
In 2018, Nornickel developed and introduced the STO KISM 121-222-2018 standard to improve control and safety of work performed by contractors at its facilities. The standard sets out relevant requirements applicable to contractors at the selection stage and onwards.
Key injury indicators 403–2
Indicator |
UoM |
2014 |
2015 |
2016 |
2017 |
2018 |
---|---|---|---|---|---|---|
FIFR |
0.07 |
0.12 |
0.11 |
0.07 |
0.05 |
|
LTIFR |
0.48 |
0.62 |
0.35 |
0.44 |
0.23 |
|
Total workplace injuries in accordance with the Russian labour laws |
pcs |
64 |
88 |
56 |
60 |
32 |
Fatal workplace injuries |
pcs |
8 |
14 |
13 |
8 |
6 |
Minor injuries |
pcs |
305 |
411 |
719 |
719 |
1,04351 |
Potentially dangerous incidents 52 |
pcs |
349 |
976 |
1,845 |
1,711 |
2,270 |
Occupational diseases |
pcs |
226 |
271 |
339 |
361 |
318 |
Total work-related accidents among the contractors’ employees engaged at the Group’s sites, in accordance with the Russian labour laws2 |
pcs |
13 |
19 |
17 |
16 |
19 |
|
pcs |
5 |
5 |
7 |
1 |
2 |
Occupational health and safety expenses |
RUB mln |
7,446 |
10,748 |
8,515 |
8,708 |
10,563 |
|
RUB thousand |
95 |
134 |
106 |
114 |
141 |
In 2018, the Company registered one fatality that took place in 2017. The fatality was further investigated and recorded on the basis of a court ruling.
In 2018, the lost time injury frequency rate (LTIFR) decreased from 0.44 to 0.23, down by 48% y-o-y, reaching the Company's record low and remaining below the industry average. The number of lost time injuries halved, from 52 to 26, while fatalities fell by 25%, from 8 to 6, on the back of initiatives to ensure compliance with core occupational safety requirements and improve safety standard management.
Fatalities breakdown in 2018 by type of accident: exposure to hazardous substances — two incidents, injuries caused by falling from heights, rockfalls in mines, impact of vehicles on pedestrians and other injuries — one incident each.
All workplace accidents are investigated in accordance with the applicable Russian laws. Investigation results serve as a basis for developing measures to be taken promptly to eliminate the root causes.
Actions to mitigate key risks
- self-propelled and drilling equipment purchased and put into operation at Polar Division’s mining facilities and Polar Construction Company (16 roof bolters, 9 concrete spraying systems, 2 concrete mixers, and 6 mechanical scalers);
- new rock bolting systems (116,221 fiberglass and 169,663 self-drilling anchor bolts) installed.
Explosion
-
automated gas control and safety systems installed to power the equipment off when explosive gas mixtures are detected in the air (59 pcs at Polar Division, 82 pcs at Medvezhy Ruchey, and 43 pcs at Polar Construction Company).
Impact of vehicles on pedestrians
- a Sandvik LH514 underground loader training simulator and a Sandvik DS 411 drill rig simulator module purchased in 2018;
- a programme developed and a simulation training organised by Norilsk Nickel Corporate University experts in collaboration with NORMET;
- the construction of the underground training base completed in December 2018 at Kayerkansky Mine.
Falling from heights
- there is a High Altitude Operations standard at the Company's facilities;
- the personnel trained for safe working at height and drilled at six training bases, with the last one commissioned at Norilsknickelremont in 2018;
- new portable fall protection anchors tested at Polar Division, Norilsknickelremont and Norilsk Support Complex;
- Permanent horizontal lifelines were tested on the field at Norilsknickelremont and PSMK as part of pilot projects.
Health and safety performance indicators for accident prevention
Indicator |
2013 |
2014 |
2015 |
2016 |
2017 |
2018 |
---|---|---|---|---|---|---|
Audits conducted: |
||||||
by health and safety committees (thousand) |
> 35 |
> 33 |
> 33 |
> 31.5 |
> 30.8 |
> 30.9 |
Target audits conducted by managers, senior specialists and committees of the Group’s facilities and business units (thousand) |
16 |
7.7 |
8.4 |
6.8 |
8.7 |
9.7 |
Ad hoc audits (thousand) |
21 |
6.3 |
8.1 |
8.8 |
15.3 |
15.7 |
Comprehensive audits of health and safety and relevant management systems |
157 |
160 |
163 |
167 |
221 |
149 |
Coupons removed from the books of employees violating health and safety requirements54 (thousand) |
6.4 |
4.4 |
3.9 |
3.4 |
2.9 |
2.2 |
Employees subject to disciplinary action for the violation of health and safety requirements (thousand) |
7.6 |
6.9 |
8.3 |
8.8 |
7.9 |
6.8 |
Employees with reduced bonus payments (thousand) |
> 17 |
> 14 |
> 15 |
> 15 |
> 13.6 |
> 13 |
total (RUB mln) |
> 67 |
> 56 |
> 55 |
> 74 |
> 70 |
|
Employees incentivised for health and safety involvement and lower workplace injury rate as per the audit results (thousand) |
> 7 |
> 5 |
> 9 |
> 5 |
> 5.6 |
> 6.4 |
total (RUB mln) |
> 42 |
> 35 |
> 78 |
> 51 |
> 41 |
> 52 |
Special assessment of working conditions
In 2018, the Company carried out a special assessment of working conditions at Polar Division, Polar Transport Division, Norilsknickelremont, Polar Construction Company, Norilsk Support Complex, Norilskpromtransport, Norilskgeologiya, NTEK, Norilskgazprom, and other production facilities, in accordance with the Federal Law On Special Assessment of Working Conditions. The special assessment of working conditions covered 7,800 workplaces and over 14,000 employees, with expenses across the Group exceeding RUB 12 mln, including some RUB 0.8 mln for MMC Norilsk Nickel.
Staff training in health and safety
In 2018, the Company arranged for the pilot testing (assessment of knowledge and skills) of line managers in charge of mines and mining facilities at Polar Division and Kola MMC as part of the project to develop and roll out a model of professional competencies for line managers of mining facilities. The results were used to assess the adequacy of the competency model.
To benefit from the opportunities offered by interactive safety briefings, comprehensive programmes were put in place enabling remote briefings for employees and testing capabilities for key mining jobs. In 2018, the programmes helped test and brief over 2,370 employees.
New employees and employees with a track record of up to three years received dedicated induction health and safety training that covered around 3,600 people in 2018.
The mines of Polar Division, Kola MMC, Medvezhy Ruchey, Norilsknickelremont and GRK Bystrinskoe installed and pilot tested the Pre-Shift Examiner software and hardware systems.
In 2018, health and safety pre-certification briefing, basic training and certification covered 34,300 employees of the Group, including 15,500 from MMC Norilsk Nickel. The Group's health and safety training expenses amounted to RUB 99.9 mln, including RUB 50.5 mln spent by MMC Norilsk Nickel.
In April 2018, Nornickel held a corporate workshop for its managers and experts in Sochi as part of the Russian Health and Safety Week. The participants discussed a number of health and safety issues and drafted roadmaps to tackle these.
In 2018, we completed the construction of the underground training base at Anhydride mine (Kayerkansky Mine).
Health and safety communications programme
The Company put in place an ongoing occupational health and safety communications programme.
In 2018, the programme focused on the following areas:
- media support of key OHS initiatives: OHS Month, drawing competitions (All Accidents are Preventable, Good Health — Great Opportunities), participation in the Russian Health and Safety Week, support for projects to control risks and implement the framework to manage technological and organisational changes, and the Workers' Control pilot project;
- a communications programme in partnership with 3M to promote the use of respiratory protection and an Underground Stories creativity contest for miners with follow-up booklets featuring the winners’ stories;
- meetings between the management of various levels and employees, media coverage on the Company’s strict compliance with OHS requirements;
- updating OHS information on the corporate portal.
Provision of personal protective equipment (PPE)
403–3As production unit employees are exposed to hazardous and harmful workplace factors (underground work, operation and maintenance of mining equipment and heavy self-propelled vehicles, extreme climate, etc.), the Company provides them with personal protective equipment (PPE) in addition to implementing technical and organisational safety measures. Employees working in contaminated conditions are supplied with free-of-charge wash-off and decontaminating agents.
To supply best-in-class PPE in line with the corporate standard, the Company’s units and the Group companies run preliminary tests on PPE, including the most advanced equipment from leading manufacturers.
To effectively monitor safe working behaviour, the Company makes employees with a track record of up to three years wear special red helmets with the word “Warning” on them and protective clothing with “Warning” badges.
In 2018, the Group purchased personal protective equipment for a total of RUB 2,563.5 mln, or RUB 40,000 per employee provided with the free PPE, including RUB 902.9 mln, or RUB 46,000 per employee spent by MMC Norilsk Nickel.
Engagement of employees in safety management
403–1
Most of the Group companies (including subsidiaries, divisions and structural production units) put in place official joint health and safety committees (councils) made up of the management, employee and trade union representatives. The Group companies running such joint committees employ over 67,800 people (around 90% of the Group's total headcount).
Authorised representatives of trade unions and staff in occupational health and safety (1,146 employees) were elected to participate in preventive activities across the Group’s production units. In 2018, they took part in over 27,000 audits and submitted more than 7,200 health and safety improvement proposals.
Health and safety topics covered in formal agreements with trade unions
403–4
The Company and most of its production units, including Kola MMC, Norilsknickelremont, Polar Construction Company, NTEK, Yenisey River Shipping Company, Norilskpromtransport and Norilsk Support Complex, entered into collective bargaining agreements with employee representatives (including trade union organisations). The collective bargaining agreements contain occupational health and safety provisions and are in place at the companies that employ some 81% of the Group's staff.
Health and safety indicators for 2017–2018
403–2
Indicator |
2017 |
Including |
2018 |
Including |
||
---|---|---|---|---|---|---|
Male |
Female |
Male |
Female |
|||
Norilsk Nickel Group |
||||||
Fatal workplace injuries |
8 |
8 |
0 |
6 |
6 |
0 |
FIFR |
0.07 |
0.05 |
||||
Lost time workplace injuries |
52 |
49 |
3 |
26 |
21 |
5 |
LTIFR |
0.44 |
0.23 |
||||
Total recorded workplace injuries in accordance with the Russian labour laws (minor + severe + fatal) |
60 |
57 |
3 |
32 |
27 |
5 |
Severe injuries |
13 |
12 |
1 |
5 |
5 |
0 |
Occupational diseases |
361 |
329 |
32 |
318 |
296 |
22 |
Occupational disease rate |
3.07 |
2.87 |
||||
Occupational injury rate55 |
0.51 |
0.29 |
||||
Lost day rate |
73.65 |
53.99 |
||||
Absentee rate56 |
3.04 |
2.93 |
||||
Total recorded workplace injuries among contractors’ employees engaged at the Group’s sites, in accordance with the Russian labour laws57 |
16 |
14 |
2 |
19 |
19 |
0 |
including fatalities |
1 |
1 |
0 |
2 |
2 |
0 |
Norilsk Industrial District |
||||||
Fatal workplace injuries |
8 |
8 |
0 |
2 |
2 |
0 |
FIFR |
0.10 |
0.03 |
||||
Lost time workplace injuries |
38 |
38 |
0 |
15 |
12 |
3 |
LTIFR |
0.47 |
0.20 |
||||
Total recorded workplace injuries in accordance with the Russian labour laws (minor + severe + fatal) |
46 |
46 |
0 |
17 |
14 |
3 |
Severe injuries |
10 |
10 |
0 |
4 |
4 |
0 |
Occupational diseases |
273 |
270 |
3 |
255 |
253 |
2 |
Occupational disease rate |
3.40 |
3.47 |
||||
Occupational injury rate |
0.57 |
0.23 |
||||
Lost day rate |
99.09 |
66.86 |
||||
Absentee rate |
3.10 |
2.96 |
||||
Total recorded workplace injuries among contractors’ employees engaged at the Group’s sites, in accordance with the Russian labour laws |
8 |
8 |
0 |
11 |
11 |
0 |
including fatalities |
0 |
0 |
0 |
1 |
1 |
0 |
Kola site (Murmansk Region) |
||||||
Fatal workplace injuries |
0 |
0 |
0 |
4 |
4 |
0 |
FIFR |
0.00 |
0.22 |
||||
Lost time workplace injuries |
4 |
3 |
1 |
5 |
5 |
0 |
LTIFR |
0.21 |
|||||
Total recorded workplace injuries in accordance with the Russian labour laws (minor + severe + fatal) |
4 |
3 |
1 |
9 |
9 |
0 |
Severe injuries |
1 |
1 |
0 |
1 |
1 |
0 |
Occupational diseases |
87 |
58 |
29 |
62 |
42 |
20 |
Occupational disease rate |
4.57 |
3.40 |
||||
Occupational injury rate |
0.21 |
0.49 |
||||
Lost day rate |
9.87 |
14.83 |
||||
Absentee rate |
3.15 |
3.33 |
||||
Total recorded workplace injuries among contractors’ employees engaged at the Group’s sites, in accordance with the Russian labour laws |
3 |
1 |
2 |
6 |
6 |
0 |
including fatalities |
0 |
0 |
0 |
0 |
0 |
0 |
Krasnoyarsk Territory (excluding NID) |
||||||
Fatal workplace injuries |
0 |
0 |
0 |
0 |
0 |
0 |
FIFR |
0.00 |
0.00 |
||||
Lost time workplace injuries |
7 |
5 |
2 |
3 |
2 |
1 |
LTIFR |
1.05 |
0.49 |
||||
Total recorded workplace injuries in accordance with the Russian labour laws (minor + severe + fatal) |
7 |
5 |
2 |
3 |
2 |
1 |
Severe injuries |
2 |
1 |
1 |
0 |
0 |
0 |
Occupational diseases |
1 |
1 |
0 |
1 |
1 |
0 |
Occupational disease rate |
0.15 |
0.16 |
||||
Occupational injury rate |
1.05 |
0.49 |
||||
Lost day rate |
53.99 |
63.13 |
||||
Absentee rate |
3.06 |
3.6 |
||||
Total recorded workplace injuries among contractors’ employees engaged at the Group’s sites, in accordance with the Russian labour laws |
2 |
2 |
0 |
0 |
0 |
0 |
including fatalities |
0 |
0 |
0 |
0 |
0 |
0 |
Moscow and other regions of Russia |
||||||
Fatal workplace injuries |
0 |
0 |
0 |
0 |
0 |
0 |
FIFR |
0.00 |
0.00 |
||||
Lost time workplace injuries |
1 |
1 |
0 |
1 |
1 |
0 |
LTIFR |
0.15 |
0.15 |
||||
Total recorded workplace injuries in accordance with the Russian labour laws (minor + severe + fatal) |
1 |
1 |
0 |
1 |
1 |
0 |
Severe injuries |
0 |
0 |
0 |
0 |
0 |
0 |
Occupational diseases |
0 |
0 |
0 |
0 |
0 |
0 |
Occupational disease rate |
0.00 |
0.00 |
||||
Occupational injury rate |
0.15 |
0.15 |
||||
Lost day rate |
48.55 |
11.24 |
||||
Absentee rate |
2.63 |
1.81 |
||||
Total recorded workplace injuries among contractors’ employees engaged at the Group’s sites, in accordance with the Russian labour laws |
0 |
0 |
0 |
0 |
0 |
0 |
including fatalities |
0 |
0 |
0 |
0 |
0 |
0 |
Trans-Baikal Territory |
||||||
Fatal workplace injuries |
0 |
0 |
0 |
0 |
0 |
0 |
FIFR |
0.00 |
0.00 |
||||
Lost time workplace injuries |
2 |
2 |
0 |
2 |
1 |
1 |
LTIFR |
0.41 |
0.33 |
||||
Total recorded workplace injuries in accordance with the Russian labour laws (minor + severe + fatal) |
2 |
2 |
0 |
2 |
1 |
1 |
Severe injuries |
0 |
0 |
0 |
0 |
0 |
0 |
Occupational diseases |
0 |
0 |
0 |
0 |
0 |
0 |
Occupational disease rate |
0.00 |
0.00 |
||||
Occupational injury rate |
0.41 |
0.33 |
||||
Lost day rate |
14.57 |
52.47 |
||||
Absentee rate |
1.53 |
1.22 |
||||
Total recorded workplace injuries among contractors’ employees engaged at the Group’s sites, in accordance with the Russian labour laws |
3 |
3 |
0 |
2 |
2 |
0 |
including fatalities |
1 |
1 |
0 |
1 |
1 |
0 |
FIFR stands for fatal injury frequency rate (FIFR = FIs/total number of hours worked * 1,000,000).
LTIFR stands for lost time injury frequency rate (LTIFR = non-fatal LTIs/total number of hours worked * 1,000,000).
Occupational disease rate is the frequency of occupational diseases/total man-hours of all of the Company’s employees in the reporting period * 1,000,000.
Occupational injury rate is the frequency of occupational injuries/total man-hours of all of the Company’s employees in the reporting period * 1,000,000.
Lost day rate is the total number of lost days/total man-hours planned for the reporting period * 1,000,000.
Absentee rate is absentee days due to incapacity of any kind/total man-days planned for the reporting period * 100%.
Emergency preparedness
403–3 103–2
The Group companies take great care in maintaining emergency preparedness, as the Group embraces mining, concentration and smelting operations, operates over 300 hazardous production facilities, and uses various hazardous substances (toxic, explosive, oxidising, etc.) in its processes.
The Company complies with Federal Law No. 116-FZ On Industrial Safety of Hazardous Production Facilities dated 21 July 1997, and ensures preparedness for emergency containment and response at hazardous production facilities.
Emergency preparedness system at hazardous production facilities
To ensure emergency preparedness, the Company drafts, approves and implements emergency management plans at hazardous production facilities (hazard classes 1, 2, 3). These plans comply with Federal Law No. 116-FZ.
The underlying document for emergency management plans is the Regulation on Containment and Elimination of Accident Consequences at Hazardous Production Facilities approved by the Resolution No. 730 of the Russian Government dated 26 August 2013.
The plans are reviewed and approved in a timely manner, their effective period being:
a) for underground mining facilities — six months;
b) for open-pit mining and concentration facilities — one year;
c) for hazard class 1 facilities — two years (excluding those specified in subclauses (a) and (b));
d) for hazard class 2 facilities — three years (excluding those specified in subclauses (a) and (b));
e) for hazard class 3 facilities — five years (excluding those specified in subclauses (a) and (b)).
The plans are subject to approval by the heads (deputy heads) of the production units that operate such facilities, and heads of professional emergency rescue services and units:
— in the Norilsk Industrial District (NID) — the Norilsk Paramilitary Mine Rescue Unit (Polar Branch of Promyshlennaya Bezopasnost), Emergency Rescue and Fire Fighting Service of Polar Division;
— in the Kola Peninsula Industrial District (KPID) — Kola MMC Emergency Rescue Service made up of two emergency rescue units (Pechenga Paramilitary Mine Rescue Unit and Monchegorsk Paramilitary Emergency Rescue Unit);
— for GRK Bystrinskoe sites — East-Siberian Branch of Promyshlennaya Bezopasnost.
Emergency containment and response plans for each hazardous production facility provide for:
a) potential scenarios for the occurrence and escalation of accidents;
b) sufficient equipment and personnel to contain and mitigate the effects of emergencies, alignment thereof with accident management requirements, and engagement of professional emergency rescue units, if necessary;
c) coordination of equipment and personnel;
d) composition and deployment of equipment and personnel;
e) procedures to ensure instant availability of equipment and personnel at the facility indicating organisations responsible for maintaining equipment and personnel at required levels of preparedness;
f) setup of on-site accident management, communication and warning systems;
g) a communication system between Polar Division units and other organisations involved in containment and response operations;
h) initial response actions once an accident occurs;
i) facility personnel and emergency rescue team actions;
j) actions taken to ensure safety of employees and residents;
k) equipment, supplies, engineering and financial support for accident management.
To stay prepared for emergency containment and response at hazardous production facilities, Polar Division and GRK Bystrinskoe signed contracts with the Norilsk Paramilitary Mine Rescue Unit (Polar Branch of Promyshlennaya Bezopasnost) and East-Siberian Branch of Promyshlennaya Bezopasnost, respectively, for mine rescue services and the maintenance of auxiliary rescue teams' equipment. Auxiliary mine rescue teams were set up at Polar Division and Kola MMC hazardous production facilities (hazard classes 1 and 2) engaged in underground mining operations, as required by Federal Law No. 116-FZ and the Procedure for Establishing Auxiliary Mine Rescue Teams approved by the EMERCOM's order No. 765 dated 29 November 2013.
Auxiliary mine rescue teams attend monthly training sessions and drills in near real conditions, with medical support provided to the personnel deployed. They include classes and training on the safe and responsible use of mine rescue equipment and first aid (including in an underground or unbreathable environment), psychological preparation, and drills with self-contained breathing apparatuses.
To teach employees how to respond to an emergency at a hazardous production facility, the Company stages drills and exercises as specified in relevant plans, and engages professional rescue services and forces (NID — the Norilsk Paramilitary Mine Rescue Unit from Polar Branch of Promyshlennaya Bezopasnost, Emergency Rescue and Fire Fighting Service of Polar Division; KPID — Kola MMC Emergency Rescue Service, GRK Bystrinskoe — East-Siberian Branch of Promyshlennaya Bezopasnost).
Pursuant to the order of the Company's President, MMC Norilsk Nickel provisions RUB 50 mln to manage accidents at its divisions’ hazardous production facilities, while Kola MMC and GRK Bystrinskoe allocate RUB 25 mln and RUB 30 mln for the same purpose, respectively.
Polar Division, GRK Bystrinskoe and Kola MMC hazardous facilities put in place surveillance, warning, communication and support systems to be fully prepared for emergency containment and response. Mines are equipped with radio and positioning systems for employees, and telemetry system for underground machinery to track their locations. Hazard class 1 and 2 facilities operate local warning systems.
Improvement of social and working conditions
The Group companies operate more than 2,100 sanitary, amenity, sports and fitness, catering, healthcare, and recreational facilities with a total area of over 340,000 sq m. The Company is committed to providing comfortable social and working conditions.
From 2003, the Group has been implementing the programme to improve social and working conditions. Since its launch, we have overhauled 253 social facilities and purchased 408 relocatable buildings, investing a total of RUB 4,876.2 mln.58
In 2018, the programme covered ten divisions and Group’s Russian companies located in Norilsk, the Taimyrsky Dolgano-Nenetsky Municipal District, and the Murmansk Region. They completed the overhaul of 25 social facilities and purchased 14 relocatable buildings to be used by employees to change, warm up and take meals. The Company renovated a total of 7,285 sq m and improved social and working conditions for 2,698 employees.
Total costs amounted to RUB 645.3 mln, including RUB 514.3 mln invested in design and overhaul, and RUB 131.0 mln spent on equipment.
The programme will be running over a mid-term horizon of three years, with investments in 2019–2021 to exceed RUB 2,000 mln. During this time, the Company expects to repair and equip over 80 social facilities.
Actual costs for the programme to improve social and working conditions, RUB mln
Repairs of social facilities in 2003–2018, 2019 (plan)
Anti-corruption
UN Global Compact Principles
Principle 10: Businesses should work against corruption in all its forms, including extortion and bribery.
Preventing and fighting corruption
103–2
Nornickel’s delivering on strategic goals is based on the trust and engagement of shareholders, investors, partners, employees, state, Russian and international business communities, and society in the Company's operations. Therefore, corruption of any nature is unacceptable.
The Company consistently builds the compliance framework focusing on priority anti-corruption areas, key actions and the role of the governing bodies.
Starting 2017, MMC Norilsk Nickel implements a revised Anti-Corruption Policy that applies to the Company’s representatives and contractors, including foreign public officials and officials of international public organisations. The respective responsibilities are stipulated in agreements made with contractors or expressly provided for by the applicable laws.
Russian companies in Norilsk Nickel Group adopt and implement their own anti-corruption regulations that are in line with the Company’s anti-corruption policy.
The Company takes all the necessary and reasonable steps to cause organisations in the corporate structure and located outside Russia to comply with the key principles and requirements of the anti-corruption policy.
205–1
The Company assesses corruption risks on an annual basis, conducting quarterly risk monitoring. In 2018, corruption risk assessments were performed across all the Group’s business units and companies. No confirmed incidents of corruption were identified.
205–2
When recruited, all of the employees are familiarised with the corporate Anti-Corruption Policy and related regulations, and starting 2015, sign addenda to their employment contracts that set out anti-corruption responsibilities. The Company has the e-learning course On Preventing Corruption in place for new employees. As at the end of 2018, the share of employees informed about the Group’s existing corruption prevention policy is 100%. In 2018, the dedicated training on the requirements and provisions of the corporate anti-corruption regulations was received by 3,505 people (4.72% of the Group’s employees as at the end of 2018).
Through the efforts of its representatives, Nornickel takes active part in developing and implementing domestic and international policies on combating corruption.
Andrey Bugrov, the Company’s Senior Vice President, is a member of a number of top-level organisations that supervise this area, in particular:
- Expert Council of the Presidential Anti-Corruption Directorate;
- B20’s anti-corruption task forces;
- Expert Council on Corporate Governance at the Russian Ministry of Economic Development;
- representative of the Russian Union of Industrialists and Entrepreneurs engaged in groups and committees of the Business and Industry Advisory Committee to the OECD (BIAC): the Anti-Corruption Task Force and the Corporate Governance Committee.
Anti-corruption matters are an integral part of the functions of other entities where Andrey Bugrov serves as a member.
Preventing and Fighting Corruption at Nornickel
Nornickel's anti-corruption initiatives are regularly covered in corporate press releases. The Company maintains the Preventing and Fighting Corruption page on the corporate website www.nornickel.com containing information on anti-corruption regulations adopted, measures taken, preventive procedures introduced, legal training sessions organised and law-abidance awareness among staff and counterparties.
Creating awareness and training of employees in the existing corruption prevention policies and methods in 2018, by region
Indicator |
Norilsk Industrial District |
Krasnoyarsk Territory (excluding the Norilsk Industrial District) |
Kola Peninsula Industrial District (Murmansk Region) |
Moscow and other regions of Russia |
Trans-Baikal Territory |
Total |
---|---|---|---|---|---|---|
Number of employees informed about the Group’s existing corruption prevention policies and methods, persons |
50,021 |
3,327 |
12,582 |
5,023 |
3,264 |
74,217 |
Share of employees informed about the Group’s existing corruption prevention policies and methods, % |
100.00 |
100.00 |
100.00 |
100.00 |
100.00 |
100 |
Number of employees trained in the existing corruption prevention policies and methods, persons |
229 |
299 |
1,672 |
1,292 |
13 |
3,505 |
Share of employees trained in the existing corruption prevention policies and methods, % |
0.5 |
9.0 |
13.2 |
25.7 |
0.4 |
4.72 |
Creating awareness and training of employees in the existing corruption prevention policies and methods in 2018, by category
Indicator |
Managers |
White-collar employees |
Blue-collar employees |
Total |
---|---|---|---|---|
Number of employees informed about the Group’s existing corruption prevention policies and methods, persons |
10,543 |
13,439 |
50,235 |
74,217 |
Share of employees informed about the Group’s existing corruption prevention policies and methods, % |
100.00 |
100.00 |
100.00 |
100.00 |
Number of employees trained in the existing corruption prevention policies and methods, persons |
531 |
1,348 |
1,626 |
3,505 |
Share of employees trained in the existing corruption prevention policies and methods, % |
5.0 |
10.0 |
3.2 |
4.72 |
Corporate Trust Service
103–2
The Corporate Trust Service was established at Nornickel back in 2010 to ensure prompt response to reported violations, abuses and embezzlement. The Service's scope of responsibility covers all business units of the Company and Group companies. The Service is governed by the Procedure on the Corporate Trust Service of MMC Norilsk Nickel approved by the Company’s President. Report statistics are submitted to the Audit and Sustainable Development Committee of the Board of Directors and the Company’s operations on a quarterly basis.
The principles underlying the Corporate Trust Service include guaranteed confidentiality for whistle-blowers, independent consideration of reports, and timely and unbiased consideration of all reports irrespective of the position and employment period of the person mentioned therein.
Nornickel’s Corporate Trust Service: toll-free hotline available 24/7: +7 800 700 1941 and +7 800 700 1945, email: skd@nornik.ru.
Information about the Corporate Trust Service is posted on the Company's official website: www.nornickel.ru, intranet site, salary slips, calendars, posters with the Service’s logo.
Persons in charge of the Service have processing performance of incoming reports as their individual KPIs.
Reports received in 2018, items (394 items in total)
Reports confirmed in 2018, items (95 items in total)
Framework for registering and reviewing reports by the Corporate Trust Service
Anti-money laundering and counter-terrorist financing initiatives
As required under Federal Law No. 115-FZ On Anti-Money Laundering and Combating the Financing of Terrorism dated 7 August 2001, the Company implements a set of anti-money laundering and counter-terrorist financing initiatives (“AML/CTF”).
The main document regulating the Company’s procedures for AML/CTF monitoring is the Internal Control Rules on Combating Money Laundering and Financing of Terrorism and Proliferation of Weapons of Mass Destruction developed in compliance with the Federal Law requirements and approved by the Nornickel President’s Order No. GMK/90-p dated 24 August 2018.
The key principle underlying the Company’s AML/CTF monitoring practices is the engagement of all employees, within their competences, in identifying signs of money laundering and terrorist financing activities in counterparties’ operations, and also in identifying operations subject to mandatory control.
The Company runs due diligence on all potential counterparties before signing contracts with them in order to check their reliability and identify entities and persons involved in extremist or terrorist activities.
Environment
UN Global Compact Principles
Principle 7: Businesses should support a precautionary approach to environmental challenges.
Principle 8: Businesses should undertake initiatives to promote greater environmental responsibility.
Principle 9: Businesses should encourage the development and diffusion of environmentally friendly technologies.
|
2018–2023 strategic cycle |
---|---|
Targets |
2020
2023
|
Environmental expenditures, RUB bn |
CAPEX for the Sulphur Project around RUB 150 bn by 2023 |
Projects |
|
Environmental Management System
Nornickel’s management considers environmental protection an integral part of the production process. The Company complies with the applicable laws and international agreements and is committed to reducing emissions, on a phased basis, and sustainable use of natural resources.
The Environmental Management System is part of the Group's integrated quality and environmental management system, which enables the Group to harmonise environmental and quality management initiatives with operations of other functions (production management, finance, health and safety, etc.). This approach is beneficial both for environmental security and for overall performance across the Company.
Environmental management at Nornickel 102–30 201–2
During 2018, the Company carried out internal audits within the framework of CIMS. In line with international standards and Nornickel’s by-laws, internal audits were conducted by specially trained and competent personnel:
- 17 EMS internal audits were held at the Company’s Head Office (as part of the CIMS internal audits);
- 70 internal audits were held at Polar Division, Polar Transport Division and Murmansk Transport Division (19, 26 and 25 audits, respectively);
- In 2018, 35 internal EMS audits were conducted at Kola MMC (as part of the CIMS internal audits).
The Company has drafted and keeps updating a register of corporate and internal auditors.
Precautionary approach
102–11
In accordance with its Investment Project Risk Management Regulations, Nornickel analyses risks and assesses impacts and potential consequences using qualified expert review during both project initiation and implementation. In the event material risks are identified, mitigation initiatives are developed, and a decision may be taken to abandon the project. During state expert review, FEED documents for all the projects being implemented by the Company undergo mandatory assessment for compliance with the applicable law.
When planning its operations, the Company ensures compliance with the requirements of the applicable Russian environmental laws and regulations.
Environmental protection expenditures
103–2 307–1
The Group’s total environmental protection expenditures stood at RUB 32.5 bn in 2018, up 117.9% year-on-year. The largest spending items were current environmental protection expenditures (RUB 19.2 bn) and capital investments to ensure environmental protection and sustainable use of natural resources (RUB 12.6 bn).
Environmental costs and expenditures, RUB mln
Expenditure item |
2016 |
2017 |
2018 |
---|---|---|---|
Current environmental protection expenditures |
15,405.17 |
20,907.06 |
19,161.00 |
Capital investments to ensure environmental protection and sustainable use of natural resources |
9,567.83 |
4,981.95 |
12,607.28 |
Charges for permissible and surplus emissions (effluents) and disposal of production and consumption waste |
745.77 |
626.79 |
695.18 |
Charges paid by the Company to remedy damages arising from non-compliance with environmental laws (excluding environmental fines) |
4.19 |
244.31 |
1.53 |
Environmental expenditures and costs |
25,722.96 |
26,760.22 |
32,464.99 |
In 2018, the Company paid a total of RUB 3,187,000 in environmental fines and received 35 improvement notices from regulators.
Performance indicators
Air protection
103–2 413–2
Norilsk is the primary area affected by multifaceted operations of Polar Division. 54 pollutants are emitted into the air in this area. The key pollutant is sulphur dioxide accounting for 98% of all emissions.
Kola MMC’s operations have environmental implications mostly for Monchegorsk and Zapolyarny towns and Nickel settlement. The key pollutants resulting from copper and nickel feedstock processing are sulphur compounds and dust containing heavy non-ferrous metals such as nickel and copper.
Reduction of air emissions (especially those of sulphur dioxide and dust containing non-ferrous metals) is the key objective pursued by the Company's operational units in terms of environmental management.
To communicate its environmental efforts to the people of Norilsk, Polar Division has been running an automatic toll-free enquiry service offering short-term forecasts on the environmental situation in the city.
To raise the stakeholders’ awareness of its large-scale environmental initiative, the Company opened a Sulphur Project showroom in 2017. The showroom functions at Nadezhda Metallurgical Plant and uses the latest exhibition technology. The exhibits include:
- architectural models of the facilities to be used to utilise sulphur dioxide emissions at the plant;
- building models with augmented reality elements to demonstrate solutions and technology;
- interactive stands providing information about the existing projects, Polar Division, Nadezhda Metallurgical Plant and the Company’s environmental initiatives;
- screens with information videos about the projects.
In 2017, a roadmap to reduce air pollutant emissions at Polar Division in 2018–2023 was developed, with Rosprirodnadzor’s approval obtained. The roadmap takes into account the current state of emission sources following the shutdown of Nickel Plant and completion of reconfiguration at Polar Division's production facilities. It covers major projects (sulphur projects at Copper Plant and Nadezhda Metallurgical Plant, and the conversion shop area upgrade at Copper Plant), timely progress on which will allow Nornickel to keep emissions down to maximum permissible rates.
Official deadlines for reaching maximum permissible emission rates at Polar Division were set forth in a decree of the government of the Krasnoyarsk Territory.
Air pollutant emissions, kt 305–7
Reduction of SO2 emissions at Kola MMC, tonnes
In 2018, the Group's pollutant emissions increased 5%, while Kola MMC’s emissions went down 3.6%.
Implementation of emission reduction initiatives in 2018
Polar Division
In 2018, the Company continued bringing emissions gradually down to below the maximum permissible concentration levels set for MMC Norilsk Nickel’s Polar Division.
One of the projects aimed at achieving this goal was completed at Copper Plant's Smelting Shop. The flue gas extraction process was rearranged to bring gas from holding furnaces, slag siphons and charging doors of Vanyukov's furnaces 2 and 3 to DT-1 flue gas stack. With the new process introduced in 2018, nearly 11 ktpa of emissions from shut-down low-height sources at Copper Plant (gas bleeders of matte and slag holding baths of Vanyukov's furnaces) were eliminated and redirected to DT-1 flue-gas stack. Estimated ground level concentrations of pollutants in Norilsk residential areas were reduced by 2.65 permissible limit values for sulphur dioxide and by 0.36 permissible value for lead.
During 2018, much work was done at Polar Division's facilities to overhaul and repair gas cleaning units, dust exhausting units and dust collectors, which resulted in the reduction of dust emissions from stationary emission sources:
- Copper Plant (Smelting Shop, Drying Shop, and PGM Concentrator): routine repair of dust exhausting units at Converters 2–7;
- Nadezhda Metallurgical Plant (Smelting Shop 1, Feedstock and Charge Makeup Shop, Elemental Sulphur Production Shop 1).
In 2018, the Company continued its efforts to control pollutant emissions during unfavourable weather conditions. During the reporting period, a total of 140 emission control interventions were made at Nornickel’s metallurgical operations.
On 28 December 2018, Deputy Prime Minister Aleksey Gordeyev approved the Integrated Action Plan to Reduce Air Pollutant Emissions in 2019–2024 that requires Polar Division to invest a total of RUB 123.2 bn to cut its gross emissions by at least 75% by 2023. Additionally, the action plan provides for the Federal Budget and the Krasnoyarsk Territory Consolidated Budget to allocate RUB 210 mln in 2019–2024 to finance Rosprirodnadzor’s and Rosgidromet’s air monitoring activities in Norilsk and Rospotrebnadzor's social hygiene monitoring system.
Kola MMC
An upgrade project started at Zapolyarny Concentrator. The project provides for the construction of a facility to separate low-grade (marketable quality) concentrate and high-grade concentrate and construction of a new building to dehydrate and ship low-grade concentrate to third-party consumers. High-grade concentrate will go through a new high-performance thickener and will be further processed at the Concentrator’s briquetting line and at Kola MMC’s smelting facilities using the existing technology. The project has environmental implications. When it is completed, the utilisation rate of Smelting Shop in Nickel will decrease substantially enough to decommission one of its ore-thermal furnaces and bring sulphur dioxide emissions in Nickel down to the maximum permissible level (31 ktpa).
In Monchegorsk, the Company continued working on the project named Nickel Electrowinning from Chlorine Dissolved Tube Furnace Nickel Powder with 145 ktpa Electrolytic Nickel Output. The project provides for the redesign of cathode nickel production in Nickel Tankhouse and replacement of the existing soluble anode electrorefining technology with nickel electrowinning from chlorine solutions. The new technology will reduce air emissions thanks to the elimination of anode smelting.
Climate risk management
Climate change risks are increasingly gaining attention of the investment and financial community. They are subject to government regulation in many countries. Russia is in the process of developing its regulatory framework in this area. As it evolves, the Company will additionally integrate these requirements into its CAPEX plans.
To minimise its impact on the climate, the Company implements a long-term strategy providing for the upgrade of its production facilities using the best available technologies, improving energy efficiency, and implementing measures that encourage energy saving and lower energy consumption. The Company’s strategy already addresses key non-financial risks, including climate risks, and factors in recent trends in this area.
The Group uses mostly low-carbon fuels in its production and power generation processes, with natural gas accounting for about 90% of fuels used. The Company also generates renewable energy at its Taimyr HPP Cascade. In 2018, the Company’s HPPs generated 51% of total power consumed in the Norilsk Industrial District. Electricity produced by the HPPs account for 44% of the Group’s total power consumption.
Nornickel has adopted a proactive approach in responding to GHG regulatory risks in Russia and abroad by:
- keeping record of GHG emissions;
- developing and implementing a corporate GHG emission management system;
- disclosing information on GHG emissions on a voluntary basis;
- monitoring domestic and international climate regulations;
- assessing the prospects of GHG reduction.
The Board’s Audit and Sustainable Development Committee examines climate change risk data published in Norilsk Nickel Group’s quarterly risk reports. The Board of Directors reviews climate risks while discussing the Company’s Environmental Development Framework and progress reports on major investment projects and treats them as a priority in setting Nornickel’s targets and development strategy. Climate change matters are overseen by the First Vice President and Chief Operating Officer.
305–1 305–4
Direct GHG emissions of Norilsk Nickel Group total about 10 mt of CO2 equivalent.59
The direct GHG emission intensity is 13.7 tonnes of CO2 equivalent per RUB 1 mln of consolidated revenue.
Use of ozone-depleting substances
305–6
The Group neither produces nor uses ozone-depleting substances (ODS), except for extremely limited amounts used as a chemical agent for laboratory-based chemical analysis as well as for filling and topping compressors in air conditioning units and carbonated water machines that produce water used as a cooling agent for medium- and low-temperature refrigerating equipment. The Company reports on the use of ODS to the Russian Ministry of Natural Resources as required.
Protection of water bodies
103–2 306–5
The Group uses water from surface and underground sources for its drinking, production and process supply needs as well as for community and shipping needs. Water is withdrawn in compliance with the pre-approved limits, without any major impacts on water bodies. No water is withdrawn either from the Ramsar Wetlands or from other protected natural areas.
The Company’s wastewater effluents generally do not exceed the pre-approved limits, including admissible impact limits, or have any major impact on biodiversity of water bodies and related habitats.
Total water withdrawal,60
mcm 303–1
Total water consumption,
mcm
In 2018, the Group’s water withdrawal61 grew 6.3% year-on-year and totalled 356.8 mcm. This was mostly associated with an increase in power generation and resulting growth of water consumption to cool turbine generating units at NTEK’s TPP 2.
Besides, the natural inflow of mine water increased by 2.3 mcm at Polar Division and Medvezhy Ruchey and by 1.3 mcm at Kola MMC.
Group-wide use of recycled water increased by 73 mcm (6.6%) due to enhanced water recycling at NTEK’s TPP 2 and Kola MMC.
Water consumed by Polar Division decreased by 48 mcm because Zapolyarny Mine and Norilsk Concentrator were transferred to the Medvezhy Ruchey mine.
Reused and recycled water makes 85.7% of total water consumed by the Group.
In 2018, the Group’s effluents grew by 17 mcm (11.4%) year-on-year and reached 164.4 mcm. This was mainly due to a 13.4 mcm increase in the discharge of standard-quality treated water used to cool turbine generating units at NTEK’s TPP 2.
The amount of effluents treated to standard quality at treatment facilities grew by 457,000 m3 (7.5%).
Pollutants in effluents discharged by Polar Division and Norilskenergo (branch of MMC Norilsk Nickel) decreased by 0.3 kt to 72.7 kt.
In 2018, Kola MMC’s effluents grew 16.45% year-on-year, mainly due to an increase in wastewater discharge at the Monchegorsk site where water intake for its production needs increased. At Zapolyarny and Nickel sites, effluents increased on the back of growing discharge of mine drainage and wastewater. Pollutants discharged grew by 5 kt as effluents increased.
Total effluents, mcm
In 2018, the Company continued implementing its plan to bring effluents in Norilsk gradually down to maximum permissible discharge rates for each controlled pollutant:
- local treatment plants were built at wastewater outlets 61 and 62 of United Motor Transport Enterprise;
- multiple activities are in progress to optimise water utilisation and disposal at Talnakh Concentrator;
- a wastewater treatment technique was developed to treat industrial effluents in the mixed storm water collector and utility tunnel of Nadezhda Metallurgical Plant;
- design documents were developed to upgrade Copper Plant’s Cooling Tower 2;
- pilot tests on the technology developed by Srednyaya Volga to treat Mayak Mine’s drained water delivered positive results; it was decided to use this technology as a basis for the Mayak Mine Water Treatment Project;
- search for an appropriate technique is in progress to treat water from Kayerkansky Open Pit and Limestone mine and utility effluents from Copper Plant; work is in progress to develop an alternative treatment method for drained water from Anhydride mine.
Waste management
MM3 103–2
Over 90% of the Group's production waste is classified as hazard class 5 waste (almost non-hazardous waste). This includes rock and overburden, tailings, and metallurgical slags. To minimise the environmental impact, mining waste and tailings are stored at special waste disposal sites and are used (utilised) at the Group’s facilities or by other licensed specialist companies. Mining waste and tailings are used to make filling compounds or smelting fluxes, construct and reinforce tailing dumps or railroad groundwork, as road filling, etc.
All of the Group’s waste disposal sites are listed on the national disposal site register. The sites are regularly monitored in line with designated environmental programmes. Tailings pits are monitored additionally as required by safety standards for hydraulic structures.
Production and consumption waste is treated in accordance with waste generation standards and waste disposal limits.
Waste generation and recycling, mt 306–2
Consumption of feedstock and materials, kt
feedstock and materials consumed: RUB 23,102,873,000
Including non-renewable feedstock and materials: 100%
Including reused feedstock and materials: 2,9%
In 2018, the Group generated 1.2 mt less waste than in 2017. The 7.55 mt reduction of waste generation at Polar Division and 1.96 mt decrease in waste recycling is explained by the spin-off of Zapolyarny Mine (both the underground and open-pit mines) and Norilsk Concentrator, which were transferred to Medvezhy Ruchey.
The year-on-year reduction of waste generation at Kola MMC in 2018, specifically the 0.3 mt decrease in overburden generation and the 0.5 mt decline in waste reuse, was due to the shutdown of open-pit operations and decreased utilisation of overburden rock to rehabilitate depleted open pits.
In 2018, Norilsk Nickel Group re-used 70% of all produced waste and is committed to increasing this share.
Per-unit indicators of environmental impact
Most per-unit environmental impact indicators of the Group show consistent downward trends.
Indicator |
UoM |
2014 |
2015 |
2016 |
2017 |
2018 |
---|---|---|---|---|---|---|
Per-unit air emissions |
t/RUB mln |
4.404 |
4.077 |
3.530 |
3.438 |
2.643 |
Per-unit water withdrawal |
thousand m³/RUB mln |
0.772 |
0.689 |
0.599 |
0.625 |
0.489 |
Per-unit water consumption |
thousand m³/RUB mln |
3.109 |
2.808 |
2.668 |
2.500 |
1.937 |
Per-unit effluents |
thousand m³/RUB mln |
0.319 |
0.277 |
0.262 |
0.275 |
0.226 |
Pollutants in effluents, per unit |
t/RUB mln |
0.308 |
0.302 |
0.352 |
0.404 |
0.319 |
Per-unit waste generation |
kt/RUB mln |
0.077 |
0.066 |
0.061 |
0.059 |
0.042 |
All RUB mln figures are hereinafter given per RUB mln of consolidated revenue.
Biodiversity conservation
103–2
Nornickel recognises the importance of biodiversity and seeks to minimise any potential negative environmental impact of its operations. The Company’s approach is documented in its Biodiversity Conservation Policy approved by the Board of Directors.
Its focus areas include land rehabilitation, cooperation with nature reserves, and reproduction of aquatic bioresources. The Let’s Do It environmental marathon plays an increasingly important role and brings together thousands of Company employees and local community members to support nature reserves, clean up certain areas, transplant young trees, and carry out other environmental initiatives.
Nornickel supports programmes aimed to study and preserve rare and endangered species listed on Russia’s Red Data Book, including Siberian bighorn sheep, polar bears, lesser white-fronted geese and others.
Land rehabilitation
The Company is developing Oktyabrskoye, Talnakhskoye and Norilsk-1 Deposits on the Taimyr Peninsula, Zhdanovskoye, Zapolyarnoye, Kotselvaara and Semiletka Deposits on the Kola Peninsula, and Bystrinskoye Deposit in the Trans-Baikal Territory.
Pursuant to the Russian laws, design documents for capital construction projects, including field development, must have a section describing environmental protection and monitoring initiatives to track changes across the ecosystem resulting from ongoing development, construction or accidents.
The Company has field development, mine liquidation and land rehabilitation project documents in place for all of its deposits, with special provisions made for rehabilitation activities. The project design documents provide for layouts, slopes, hydraulic and irrigation structures, and other technical measures. Importantly, the Company’s deposits are in commercial development, exploration or production test stages with liquidation or abandonment not expected until 2050.
The Company complies with all applicable regulations for land rehabilitation and other environmental protection initiatives associated with field development, construction and other operations.
Environmental protection and monitoring measures taken during the deposit life cycle 304–3 MM1
Disturbed and rehabilitated land area in 2018, ha62
Indicator |
Total |
Including |
|
|||
---|---|---|---|---|---|---|
during mining |
during construction |
during disposal of solid domestic and industrial waste |
during other activities |
|||
Total disturbed area, beginning of period |
14,889.43 |
13,225.82 |
428.95 |
66.34 |
1,168.32 |
|
Total rehabilitated area |
31.70 |
31.70 |
0.00 |
0.00 |
0.00 |
|
Total disturbed area in the reporting period |
0.10 |
0.10 |
0.00 |
0.00 |
0.00 |
|
Total disturbed area, end of period |
14,915.33 |
12,724.32 |
430.75 |
591.84 |
1,168.40 |
Nornickel traditionally takes part in urban greening projects in Norilsk, Dudinka, Monchegorsk, Zapolyarny, and Nickel. The disturbed area reclamation programme is implemented in cooperation with local authorities and volunteers and seeks to clean up and improve public spaces and areas around motorways, protect water bodies and water reserves, and revamp tourist camping sites.
In 2003, Kola MMC started implementing a land rehabilitation programme as advised by nature reserves. In just 14 years, Kola MMC had over one million trees and bushes planted over an area of about 100 ha, including as part of a pilot project to restore damaged land adjacent to the Company’s production site in Monchegorsk implemented jointly with Kola Science Centre of the Russian Academy of Sciences.
Cooperation with nature reserves
304–1 304–2
Kola MMC is located 15 km from the Pasvik Nature Reserve and 10 km from the Lapland Biosphere Reserve, while Polar Division's sites are some 80–100 km away from the buffer zone of the Putoransky Nature Reserve. Bystrinsky GOK is located 160 km away from the Relict Oaks State Reserve (the Trans-Baikal Territory). At present, the Company’s operations do not produce any significant impact on areas that are in relative vicinity to the nature reserves and areas of high biodiversity value outside protected areas. The Company’ cooperation with nature reserves focuses on developing research and technology and supporting their social, volunteering and environmental awareness programmes.
Taimyr Peninsula
The Putoransky State Nature Reserve has been on the UNESCO world heritage list since 2010. It is one of the biggest nature reserves in Russia with a total area of over 1,887,000 hectares. The reserve is part of the Joint Directorate for Taimyr Nature Reserves, which also includes the Taimyrsky and Big Arctic reserves, as well as the Purinsky and Severozemelsky natural protected areas.
The Joint Directorate for Taimyr Nature Reserves implements environmental projects selected under Nornickel’s World of New Opportunities charitable programme to support socially important initiatives. The projects focus on raising environmental awareness, environmental protection, engagement of local communities, land improvement, and landscaping.
In 2018, the Company helped Taimyr’s nature reserves to organise environmental raids and transport research groups to remote locations.
Kola Peninsula
The Company cooperates with the Lapland and Pasvik Nature Reserves in multiple areas. The key ones are environmental monitoring and vegetation restoration in the vicinity of Kola MMC's production sites.
The Pasvik State Nature Reserve is featured as one of the Wetlands for the Shadow List of Ramsar Sites under the name of Fjarvann — Schaanning’s Field Base. It covers a total area of over 14,000 ha. Pasvik is the only Russian nature reserve holding the EUROPARC Federation’s certificate, which is awarded to the best protected areas worldwide. Such certification is an important condition for international cooperation with foreign nature reserves.
Since 2006, the Pasvik Nature Reserve has been carrying out an assessment of the natural environment in the area of Pechenganickel Plant (including Zapolyarny, Nickel and their suburbs, as well as the Pasvik State Nature Reserve), and developing a long-term environmental monitoring programme. The reserve is also working on several projects that received grants under the World of New Opportunities charitable programme. The projects seek to reach out to Russian and Norwegian audiences and cover a variety of topics, including traditional use of natural resources, raising environmental awareness among schoolchildren, and promoting research. In 2018, the Company donated a mobile environmental laboratory that is based on a four-wheel drive KAMAZ vehicle and fully adapted to work in the Arctic conditions.
Pasvik’s Visitor Centre, which was built with support of the Company, is an international platform for academic forums and educational activities focused on environmental protection issues.
Red List species found in the Pasvik, Lapland and Putoransky Nature Reserves, pcs
304–4
Indicator |
Pasvik |
Lapland |
Putoransky |
---|---|---|---|
On the IUCN Red List, of which |
36 |
23 |
13 |
Critically Endangered (CR) |
0 |
0 |
0 |
Endangered (EN) |
1 |
1 |
1 |
Vulnerable (VU) |
2 |
0 |
3 |
Near Threatened (NT) |
1 |
0 |
1 |
Least Concern (LC) |
32 |
22 |
8 |
On Russia’s Red Data Book, of which |
21 |
24 |
14 |
1 — Endangered |
0 |
0 |
0 |
2 — Decreasing Number |
1 |
11 |
- |
3 — Rare |
7 |
12 |
3 |
4 — Uncertain Status |
11 |
1 |
8 |
5 — Rehabilitated and Rehabilitating |
2 |
0 |
3 |
On the Murmansk Region’s and Krasnoyarsk Territory’s Red Data Books |
107 |
166 |
13 |
With an area of 278,000 ha, the Lapland State Nature Biosphere Reserve is one of the largest protected areas in Europe and also one of Russia's oldest nature reserves (founded in 1930). In 1985, it was included in the UNESCO Network of Biosphere Reserves.
In 2002, Kola MMC and the Lapland Biosphere Reserve signed contracts for the development of a methodology to reclaim disturbed natural environments in the areas affected by permanent emissions from Severonickel Plant and monitoring of the Monchegorsk District and the Lapland Biosphere Reserve. Research results provided a basis for further rehabilitation of disturbed lands and for sanitary and fire protection improvements in forest areas.
The Company supported creation of multiple ecotrails, including the first ecotrail for children called “A Curious Child out in the Woods,” and publication of books on the reserve founders.
In the Rybachy and Sredny Peninsulas Natural Parks, environmental routes and information facilities are developed on the territory covering over 83,000 ha under an agreement between the Company and the Murmansk Region Government.
Trans-Baikal Territory
The oak grove in the Gazimuro-Zavodsky District is Siberia’s only grove of natural origin that has survived to the present day. The grove spans 30,000 ha and is located along the Argun River. As part of the agreement with the region's government, Nornickel provides financial aid in effectively protecting and exploring the ecosystems within the Relict Oaks State Reserve. The Company financed the acquisition of video monitoring devices and camera traps for the reserve. It also plans to help put in place research facilities and run educational programmes for children and adults.
Reproduction of aquatic bioresources
The Company provides annual financing for the measures to breed valuable fish species, including those listed on Russia’s Red Data Book, and release them into natural water bodies. Every year, certain populations of juvenile Siberian sturgeon and grayling are released into the Yenisey River in the Krasnoyarsk Territory; Atlantic salmon is released into the Umba River in the Murmansk Region. Specialised fish farms and research institutions are engaged in taking these measures. Another “green” project to restore and preserve the fish population will be implemented in the Trans-Baikal Territory.
Impacts from transport operations
Fleet |
Transported products |
Social and environmental responsibility |
Outcome |
---|---|---|---|
Group’s own fleet |
.normal p{
margin: 0 0 10px !important;
Products of the Group companies Products procured to meet the Group’s internal needs Commercial and social cargo |
Compliance with international conventions, codes, guidelines, Russian laws, regulations and requirements Four freight-forwarding licences, all environmental permits in place Multi-stage control from the Group companies, other transportation participants and supervisory bodies Security and industrial health and safety management systems in place at facilities |
No significant environmental impact produced by the Company's freight and personnel transportation |
Fleet chartered by the Group's Metal Trade Overseas |
Norilsk Nickel Group’s products |
Compliance of the fleet's environmental parameters with the requirements of international environmental conventions |
The Company’s fleet is regularly inspected for ship safety and compliance with licence requirements by the authorities of Russian ports and ports of call, Russian Maritime Register of Shipping, Federal Service for Transport Supervision, and Rospotrebnadzor’s Directorate.
The Group’s transport and logistics subsidiaries and units have all the necessary environmental permits and strictly adhere to the applicable environmental regulations by:
- ensuring that air pollutant emissions from mobile sources do not exceed the maximum permissible concentrations;
- purchasing marine fuels from vendors that have all the required documents on fuel quality as confirmed by an independent laboratory;
- certifying onboard wastewater treatment plants on an annual basis to prevent pollution and contamination of water bodies and marine environment;
- transferring oil-containing water to specialist contractors at sea ports;
- transferring waste promptly to specialist contractors for utilisation, treatment or disposal to prevent negative environmental impacts;
- treating their food waste and dry waste onboard in compliance with MARPOL 73/78.
Impacts from foreign operations
Norilsk Nickel Harjavalta has necessary environmental permits and an integrated management system certified to ISO 9001, ISO 14001, and OHSAS 18001. Norilsk Nickel Harjavalta’s main environmental impact consists in the emissions of ammonia (NH3) and nickel (Ni), and discharges of nickel, sulphates (SO42-) and ammonia ions (NH4+)
Environmental impact metrics of Norilsk Nickel Harjavalta
Indicator |
2016 |
2017 |
2018 |
---|---|---|---|
Industrial wastewater (thousand m3) |
771 |
899 |
988 |
Pollutants in industrial wastewater (t) — Ni — SO42- — NH4+ (rebased to nitrogen) |
0.4 22,457 49.5 |
0.5 25,853 60.3 |
0.6 30,189 70 |
Total water consumption (mcm)* |
10,9 |
11,1 |
11,8 |
Total air pollutant emissions (t) — Ni — NH3 |
71.6 1.6 70 |
70.7 1.7 69 |
85.2 1.2 84 |
Waste generation (kt) |
7.0 |
5.5 |
2.8 |
Waste disposal (kt) |
0.8 |
0.8 |
1.1 |
Power consumption (GWh) |
180 |
182 |
209 |
Power consumption for heating/cooling (GWh) |
130 |
145 |
150 |
Steam consumption (GWh) |
225 |
235 |
327 |
Environmental expenses, USD mln |
2.7 |
1.0 |
0.7 |
* Over 95% is water withdrawn from surface sources (Kokemäenjoki River).
In 2018, Norilsk Nickel Harjavalta met all permit requirements for emissions, discharges and waste disposal volumes. Lower waste volumes resulted from switching to the Company’s feedstock that is less contaminated with impurities as compared to third-party materials. The increase in effluents and pollutant emissions was driven by the growing output.
Energy saving and energy efficiency
103–2
The Company’s distinguishing feature is that most of its production facilities and workforce operate and live in the harsh Arctic climate. Nornickel uses an integrated approach to the energy infrastructure development, combining goals of reliability improvement with those of low-carbon economy. Nornickel makes continuous efforts to reduce consumption of such fuels as diesel fuel, coal and natural gas, as well as to provide its subsidiaries with reliable and efficient energy sources in the long term.
The Company’s priority renewable source of energy is hydropower generated at the Ust-Khantayskaya and Kureyskaya HPPs (481 MW and 600 MW of installed capacity respectively). These unique HPPs are among the world's northernmost ones constructed in the Arctic. The use of other renewables such as solar, geothermal and wind energy is constrained by geographic factors, such as long polar night and unsteady wind intensity.
Development of the fuel and energy assets is governed by the Fuel and Energy Development Strategy and the Programme to Upgrade, Revamp and Replace the Norilsk Industrial District’s Power Facilities through 2025. For the purposes of implementing a uniform R&D policy and meeting the targets of the Fuel and Energy Development Strategy, the Company established an energy section with its R&D Council.
Electricity and fuel resources throughput and consumption by the Group, TJ 302–1 302–3
No. |
Indicator |
2014 |
2015 |
2016 |
2017 |
2018 |
---|---|---|---|---|---|---|
1 |
Fuel consumption |
162,301 |
161,710 |
172,425 |
156,56963 |
148,910 |
2 |
Energy from renewable sources (HPPs) |
11,900 |
17,027 |
11,856 |
12,414 |
14,877 |
3 |
Electricity and heat procurement from third parties |
15,547 |
15,528 |
8,968 |
10,483 |
10,931 |
4 |
Electricity and heat sales to third parties |
20,440 |
17,918 |
19,882 |
19,503 |
18,926 |
5 |
Group's total energy consumption |
169,308 |
176,347 |
173,367 |
159,962 |
155,792 |
Energy intensity, GJ/RUB mln64 |
371 |
348 |
316 |
298 |
214 |
Fuel consumption by the Group, TJ
Indicator |
2014 |
2015 |
2016 |
2017 |
2018 |
---|---|---|---|---|---|
Fuel consumption |
162,301 |
161,710 |
172,425 |
156,568 |
148,910 |
Natural gas |
146,200 |
145,266 |
151,081 |
134,709 |
129,335 |
Coal |
4,417 |
4,170 |
2,132 |
1,460 |
1,660 |
Diesel fuel and fuel oil |
11,684 |
12,274 |
15,423 |
15,221 |
13,788 |
Gasoline and aviation fuel65 |
— |
— |
3,789 |
5,178 |
4,127 |
To achieve its energy development goals and targets, the Company runs investment projects approved by the Investment Committee. In 2018, the Company continued to enhance the reliability of generating equipment, grid and gas transportation infrastructure and boost gas output.
The Ust-Khantayskaya HPP is implementing a large-scale project to replace equipment in hydroelectric units. The fourth unit was commissioned in 2018. In 2012, the Company made a decision to replace adjustable blade hydroelectric units that had been operating for over 40 years. The new units boast better reliability and a service life of at least
50 years.
The Company was also implementing its Polar Division Energy Saving and Energy Efficiency Programme for 2013–2018, which was approved by Polar Division’s First Deputy Director and Chief Engineer.
Each year, the Company develops and implements organisational and technical action plans to save fuel, heat, power and water.
Fuel and energy savings resulting from energy consumption reduction and energy efficiency improvement initiatives, TJ 302–4
No. |
Indicator |
Polar Division |
NTEK |
Kola MMC |
---|---|---|---|---|
1. |
Total savings |
1,674 |
378 |
1,046 |
|
including |
|
|
|
1.1. |
Electric power |
315 |
8 |
206 |
1.2. |
Heat in water and steam |
220 |
217 |
25 |
1.3. |
Fuels |
1,138 |
152 |
815 |
|
including |
|
|
|
1.3.1. |
Coal |
0 |
22 |
22 |
1.3.2. |
Natural gas |
1,138 |
130 |
0 |
1.3.3. |
Diesel fuel and fuel oil |
0 |
0 |
793 |